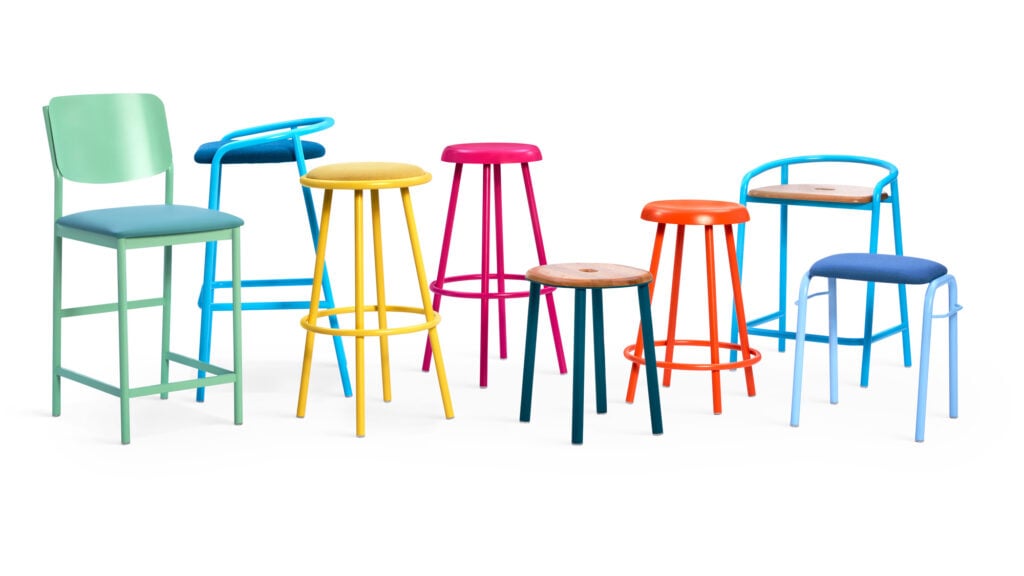
September 2, 2021
Biodegradable and Renewable Polyurethanes Are Around the Corner
Polyurethane (PU) is a victim of its own success, at least when it comes to sustainability. Comparatively inexpensive, it is one of the few polymers that can reliably stretch (it forms the basis of spandex and Lycra), can be easily foamed, and offers a highly durable and water-resistant surface for fabrics and hard surfaces alike. This means it has been nearly impossible to replace PU with other materials for the same performance and value. Flexible PU foams are everywhere, in bedding, cars, and cushioned seating, as well as in many medical, sportswear, and military applications.
So what do you do if you can’t beat the material? In recent years, scientists have had some early breakthroughs in re-creating it using renewable resources.
As with many polymers, PU is produced by the combination and reaction of two chemicals—a polyol and an isocyanate. We have known for a while how to make polyols from bio-based sources, like soybeans and other plants, or from waste CO2. But there has been no easy way to create the isocyanate from renewable sources. So only about 30 percent of any PU foam marketed as “sustainable” or “soy” is biobased, while the rest is composed of a petroleum-based chemical.
Renewable Polyurethane
Polaris Renewables has been able to bypass the need for isocyanate completely by reacting synthesized fatty acids with captured atmospheric CO2 and then polymerizing the material using bio-based amines rather than isocyanates. Although initial work focused on algae oils for the unsaturated fatty acids, Polaris is looking at cheaper and more readily available options like linseed oil and used fats, oils, and greases.Polaris’s non-isocyanate polyurethane (NIPU) is the first and currently only commercial-scale solution to take this route, with promising performance and durability attributes that are comparable to standard PU. Interest and funding from the U.S. Department of Energy, Patagonia, the bed producer Tempur Sealy, and biotech start-up Algix are enabling Polaris to make inroads into the fashion and consumer product industries.
Biodegradable Polyurethane
The inventors of Soleic biodegradable PU foam forflip-flops and surfboards call petroleum “ancient algae”—referring to the original source of fossil fuels. It’s their way of advocating their algae-based foams as replacements for PU foam in consumer products, and potentially in seating and bedding. The company purchases the raw material from algae farms and extracts oil from the aquatic plants in the same way other bioplastic producers do from soybeans and castor beans. The result is a chemically equivalent polymer that can be applied similarly to other PU foams. Its main disadvantage is that in harsher environments it could degrade into food for bacteria and other organisms quite quickly—its weight can be reduced by half after eight weeks buried in soil, for example.
Nonetheless, expect to start seeing some of these renewable and biodegradable polyurethanes in your products soon and mark one more milestone in our evolution away from fossil fuels.
Andrew Dent is the EVP of materials research at Material ConneXion and chief material scientist at Material Bank.
Would you like to comment on this article? Send your thoughts to: [email protected]
Latest
Profiles
BLDUS Brings a ‘Farm-to-Shelter’ Approach to American Design
The Washington D.C.–based firm BLDUS is imagining a new American vernacular through natural materials and thoughtful placemaking.
Projects
MAD Architects’ FENIX is the World’s First Art Museum Dedicated to Migration
Located in Rotterdam, FENIX is also the Beijing-based firm’s first European museum project.
Products
Discover the Winners of the METROPOLISLikes 2025 Awards
This year’s product releases at NeoCon and Design Days signal a transformation in interior design.