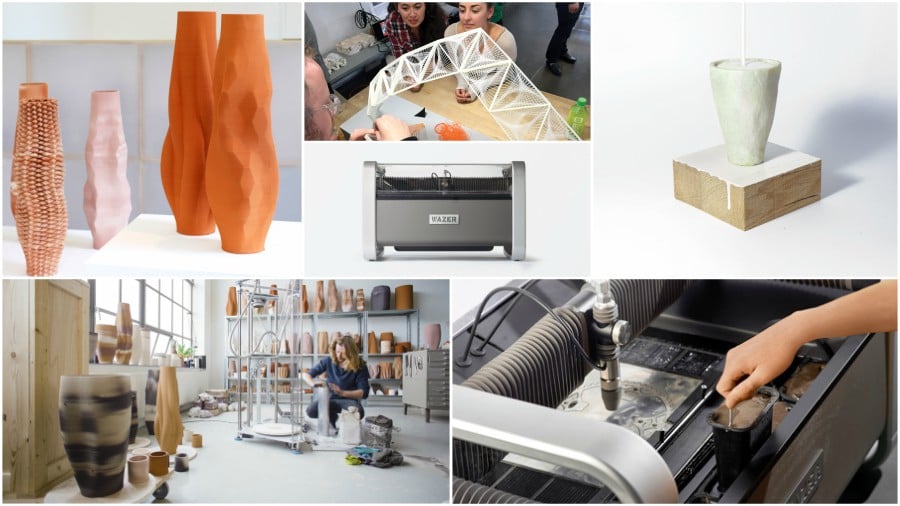
March 23, 2017
The Materials & Tools Taking Making Into the Future
The relationship between digital technology and craft underwent a rapid transformation from antagonistic to symbiotic in the past decade. Now a vanguard of makers, entrepreneurs, and institutions is taking the next step.
Materials : Protein
Tessa Silva-Dawson/London
“I thought, ‘Surely, this can be made from liquid milk,’” recalls Tessa Silva-Dawson, when she discovered casein formaldehyde, a precursor of plastic derived from powdered milk. The material, once used as an alternative to tortoiseshell and ivory, had faded from use in the 1940s when polymer-based plastics became the industry standard. In what began as her master’s thesis project at London’s Royal College of Art, Silva-Dawson’s ongoing material investigation, called Protein, seeks to revisit the sustainable potential of casein plastics with a rigorous, cradle-to-grave approach to craft.
“I was acting as half designer, half cook,” she says, describing her early trial-and-error experiments involving vinegar, enzymes, linseed oil, and glycerin—all used to isolate the proteins found in raw skim milk. She eventually arrived at a workable texture she likens to chewing gum or Play-Doh, then consulted with scientists from the British Plastics Federation to organically render the material more durable for design applications. Though technically a casein plastic, Protein has a range of properties. It can be injection-molded, similarly to thermoplastics; hand-formed, rolled, or pressed like clay; dyed and combined to create a terrazzo-like coloration pattern; machined and finished like wood; or simply left raw to
dry to the texture of grainy concrete.
“Plastic has a reputation for being cheap,” says Silva-Dawson. “This project is about getting the public to rethink where their daily objects come from, their value, and the process it takes to create them.”
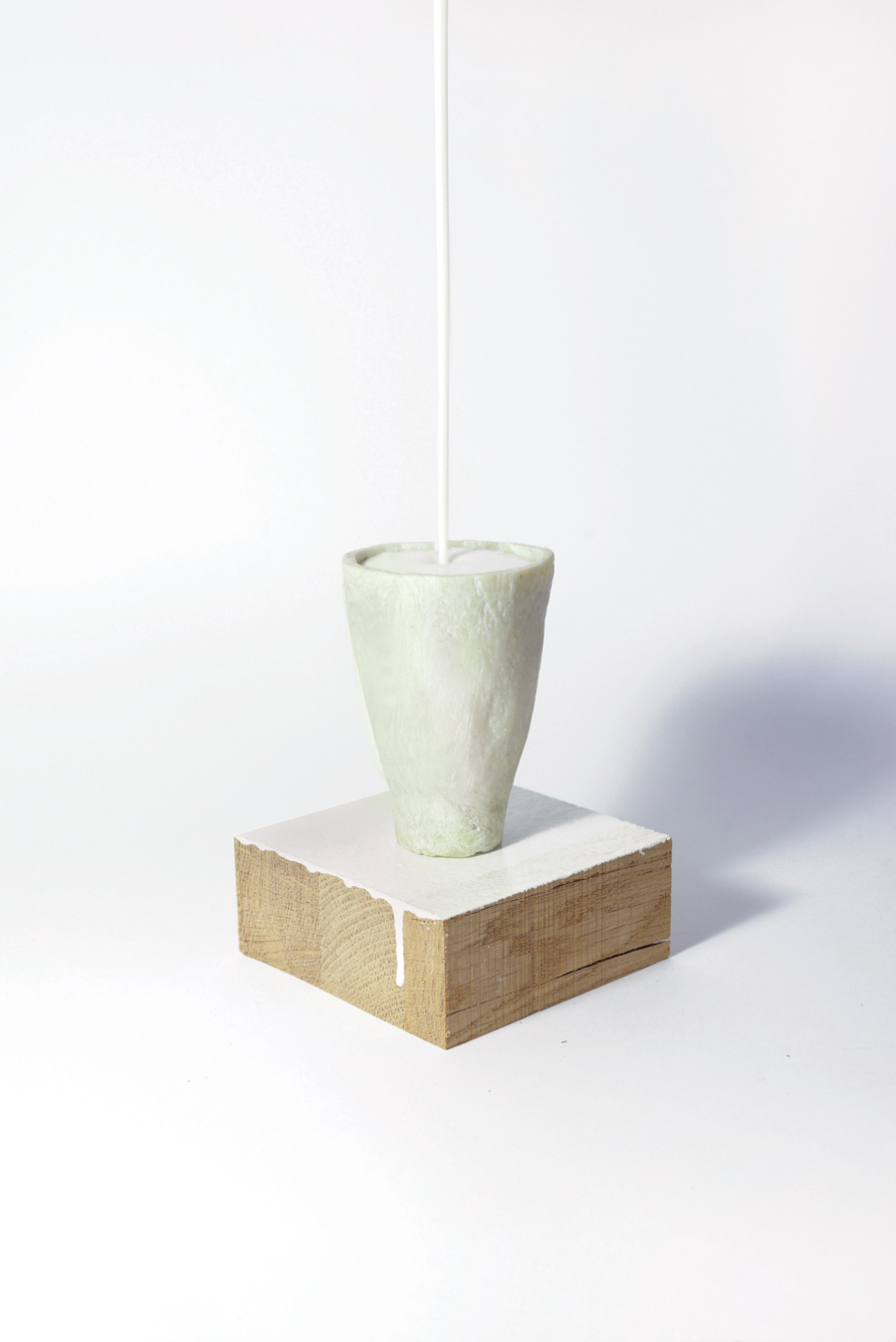
Architecture : Digital Craft Lab
California College of the Arts/San Francisco, California
As practicing architects working at the experimental frontier of tech and design, California College of the Arts professors Jason Kelly Johnson and Andrew Kudless sought a new type of hybrid creative space on campus. “The typical architecture studio has involved an individual sitting at a desk, drawing or working on a computer,” says Kudless, who together with Johnson spearheaded the opening of the Digital Craft Lab four years ago. “If you look at other models—say, furniture making—the designer is in and among all the tools, going back and forth between making, prototyping, finishing, and so forth. We wanted to provide that type of environment.”
Outfitted with rapid-prototyping equipment, the space acts as both a hands-on fabrication lab and a classroom where Johnson and Kudless teach studio courses like Creative Architecture Machines and Autonomous Architectures, in which students develop robotic machines that can build full-scale prototypes. The lab also holds lectures and workshops, as well as research initiatives with corporate partners: In 2015, Autodesk sponsored Buoyant Ecologies, a studio course asking students to imagine resilient, floating structures that could double as marine ecological systems. Two of those projects went on to win AIA COTE Top Ten for Students awards last spring, and Autodesk returned in the fall to sponsor the Creative Architecture Machines course.
As leaders of independent studios—Johnson is cofounder of an experimental design office called Future Cities Lab, and Kudless runs a hybrid architecture and computation-focused practice called Matsys—both designers have a clear vision of the sort of skill set the lab hopes to attract and foster. “We want to shift the perception that working with digital tools is a hands-off approach, that software and fabrication tools are autonomous and don’t require a physical craft,” says Johnson. “A lot of the work we produce is very much about going under the hood of things, working with ‘messy computation.’ We believe that’s the future of architecture.”
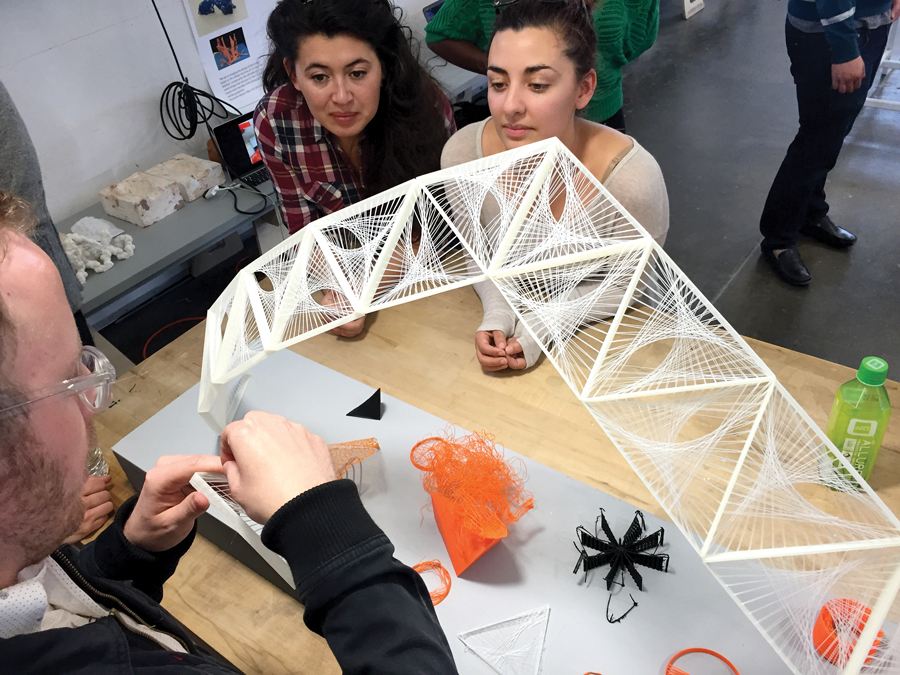
Manufacturing : Wazer
Nisan Lerea and Matthew Nowicki/New York and Shenzhen
While building racecars and robots as undergraduates at Penn Engineering, Nisan Lerea and his classmates picked up on a growing need in the manufacturing landscape. “We lacked a fast and easy way to make precision parts in sheet metal,” says Lerea, articulating the speed and cost hurdles of sending a custom one-off part to be fabricated in an industrial water jet-cutting shop, which can charge hundreds of dollars for just a single 10-by-10-inch cutout. Desktop laser-cutters, meanwhile, are limited to softer materials such as wood, plastic, or leather. When Lerea and his classmate Matthew Nowicki realized a desktop equivalent didn’t yet exist for water jet-cutting machines—which handle hardier materials including carbon fiber, stone, glass, metal, and ceramics—they built their own low-cost model for the school by the time they graduated.
Five years, a shared stint at off-grid energy start-up BioLite, and an immensely successful Kickstarter campaign later—one that surpassed its goal 13-fold, bringing in over $1.3 million— Lerea and Nowicki are now gearing up to ship the first few hundred units of their product, Wazer, to their first backers this fall.
Compact enough to fit atop a workbench or office desk, this version was refined over a months-long residency at HAX, a leading accelerator in Shenzhen, China. Priced at just under $6,000 (around $4,500 for the desktop version in the current pre-sale phase), the svelte machine is a steal compared with traditional water jets—which can cost upwards of $100,000–and makes precise cuts as narrow as 1/16th of an inch in metal, glass, and stone. “In the long term, there’s a lot of room between the style of machine we have and what exists on the industrial scale. There’s a lot of space for innovation,” says Lerea, whose lean, five-man team is rapidly growing and refining the machine’s custom software in the coming months. “We’re excited to get these machines out to customers as soon as possible.”
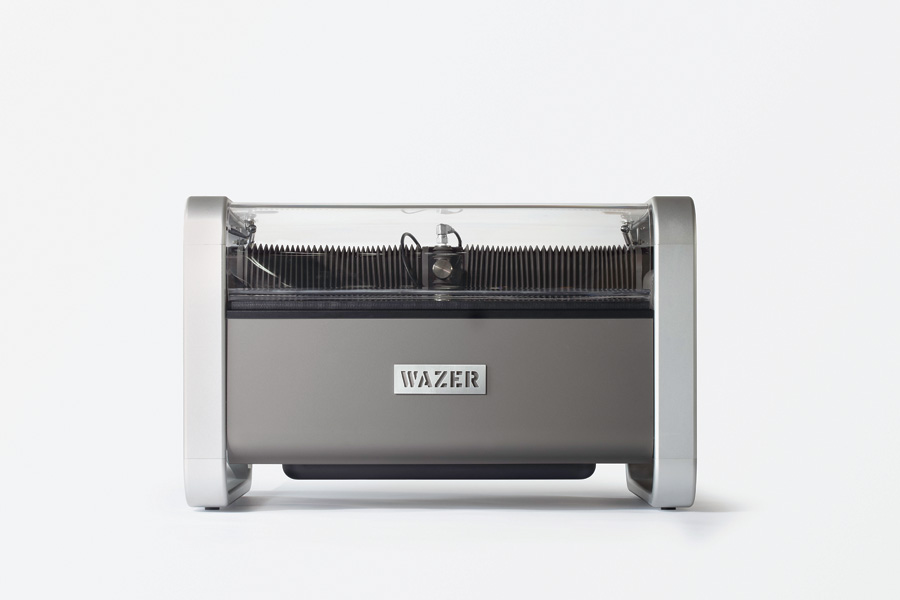
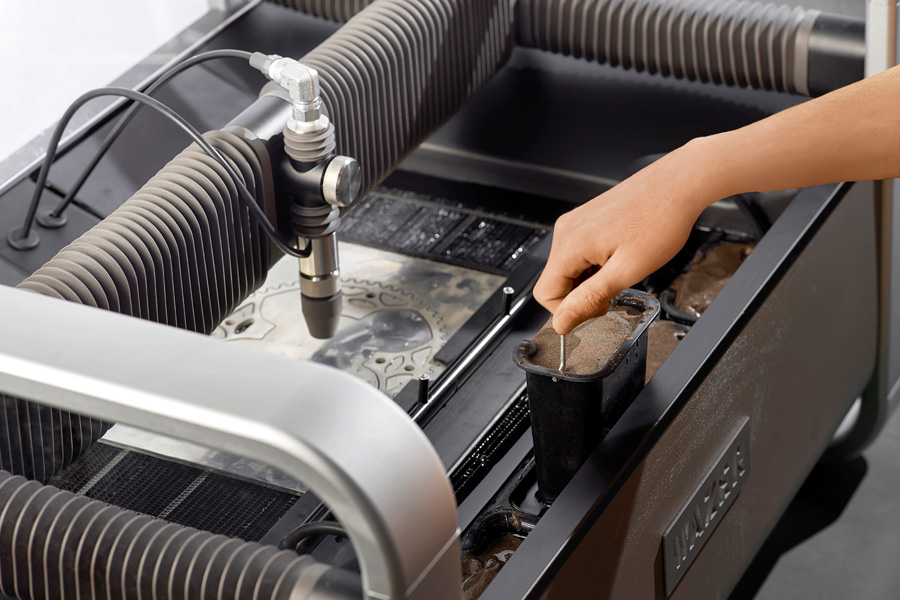
Machines : Functional 3D-Printed Ceramics
Olivier van Herpt/Eindhoven, The Netherlands
Young designers are reinvigorating the craft of ceramics, but not all of them have taken to the potter’s wheel: Olivier van Herpt, a recent graduate of Design Academy Eindhoven, has pioneered not only a new formal vocabulary with his highly intricate, otherworldly vessels, but the very apparatus by which he crafts them. As a student, van Herpt had come to regularly experiment with 3D printing, a technology that excited him, but he began to question its constraints. “To create a highly custom object, wait for hours to have it produced, and have it be made of plastic,” he says, “was a little disappointing.”
Searching for “a more noble material” that could lend itself to functional objects—something heat-resistant, durable, and food-safe—led him to explore clay. “Each type of clay comes from a different region, and when you make an object from it, it imbues it with a kind of soul,” he explains. “I became really interested in how clay might be combined with new technology, to see what might come of that transformation from digital to physical.” After many experiments with modifying existing machines, van Herpt, a trained graphic designer and clear autodidact, finally fashioned a custom 3D clay printer for his graduation project in 2014, an endeavor that he has continued to toy with and refine.
The tall, elegant machine worthy of a Westworld set (which van Herpt says will be available for purchase this spring, at $36,000 a unit) can produce vessels up to three feet high with nearly indiscernible striations, and has been exhibited widely at design fairs and museums throughout Europe and beyond. But the machine’s true value comes from its subtle imprecisions: Light, poetic irregularities mark each minuscule layer, overturning any arguments about technology’s deleterious effects on wabisabi— and making a case for the machine’s place in craft. As van Herpt says, “Each machine carries its own signature.”
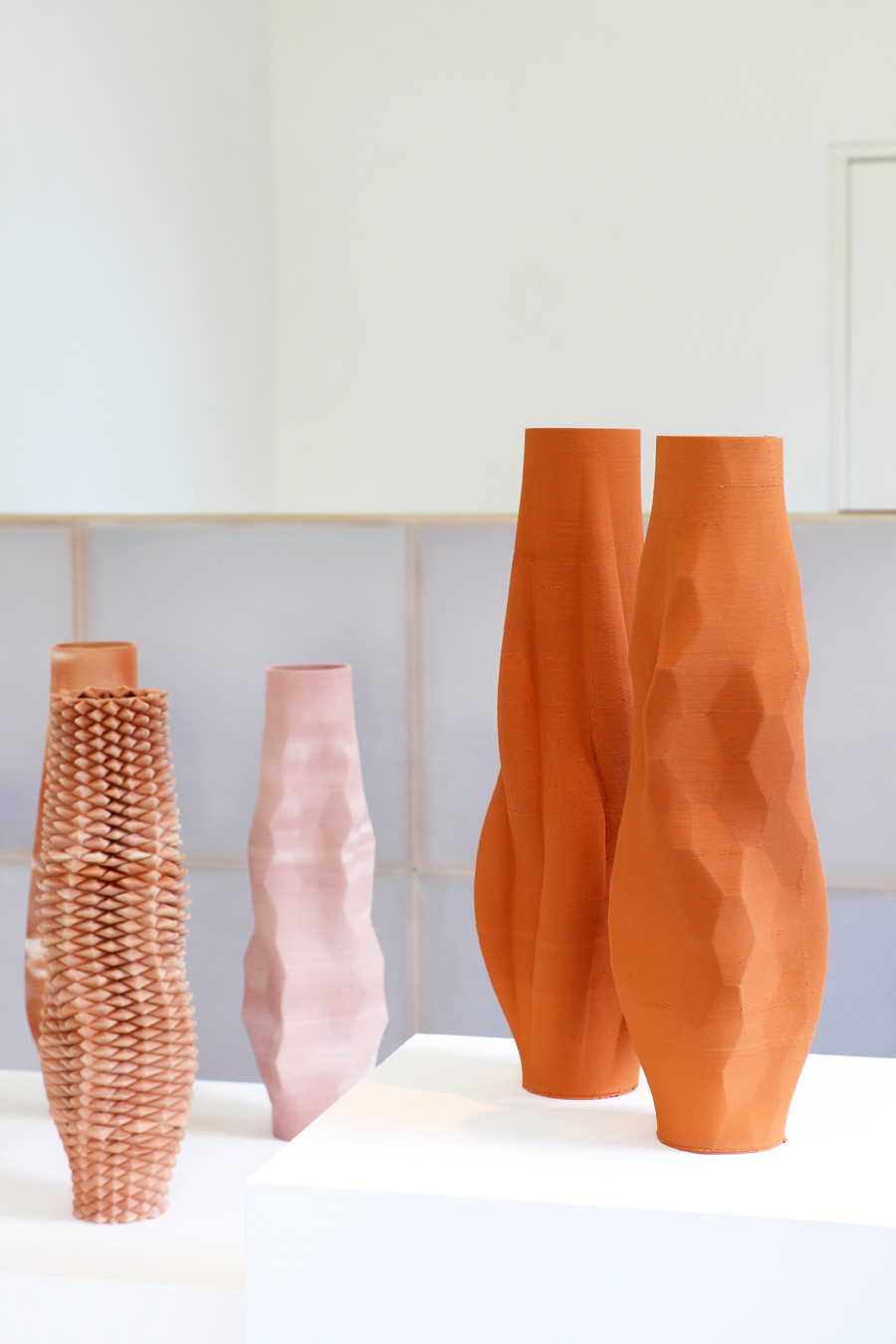
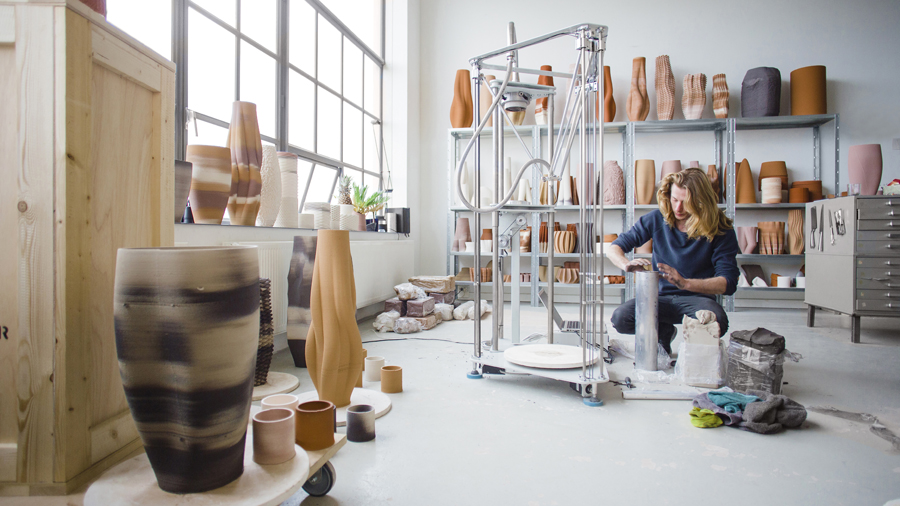