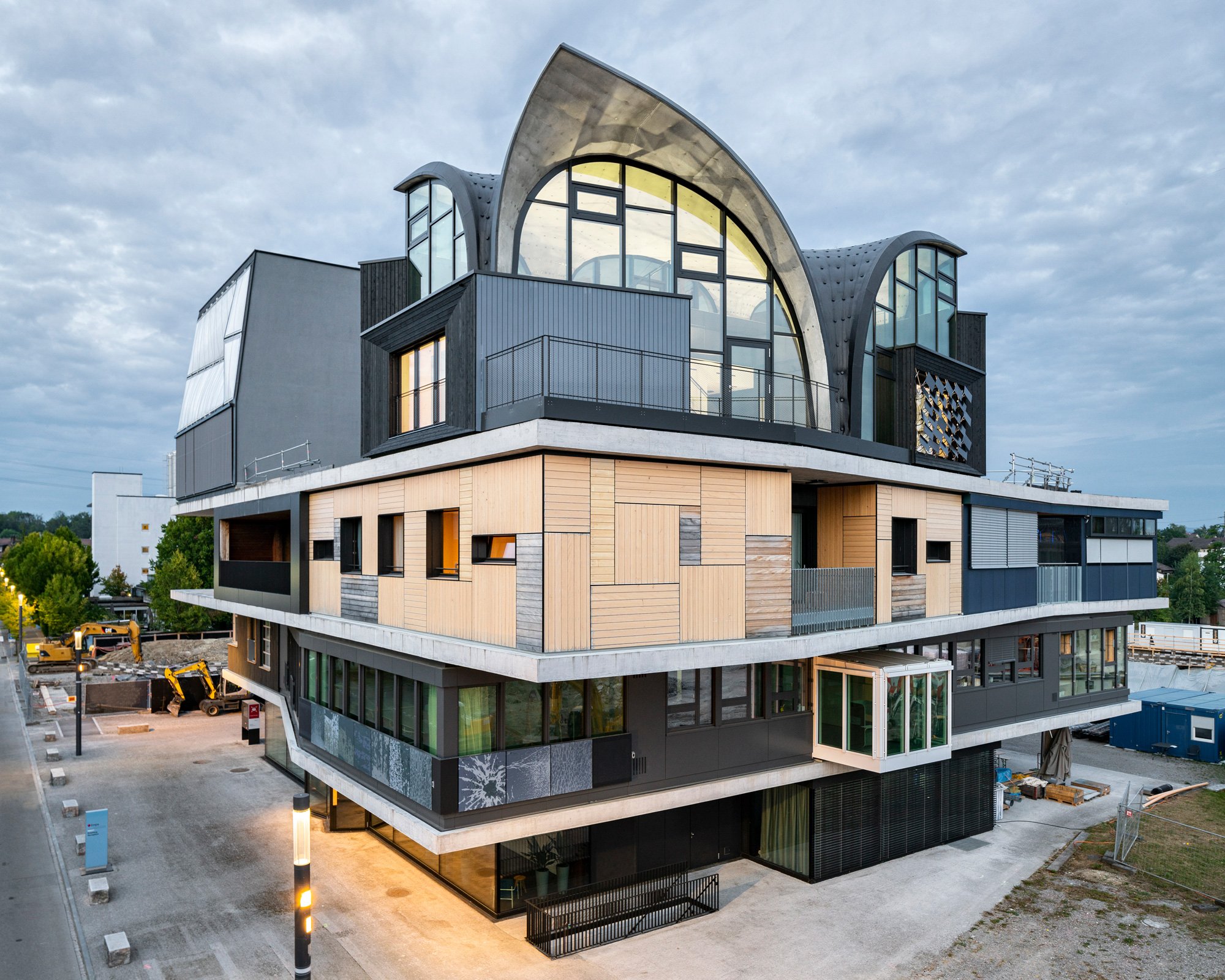
January 13, 2022
ETH Zurich’s HiLo Unit Raises the Bar for Sustainable Concrete Design
“These curved geometries span space more efficiently, with much less material, all while keeping the materials separated so they can be easily recycled at end of life.”
Dr. Tom Van Mele, Block Research Group senior scientist
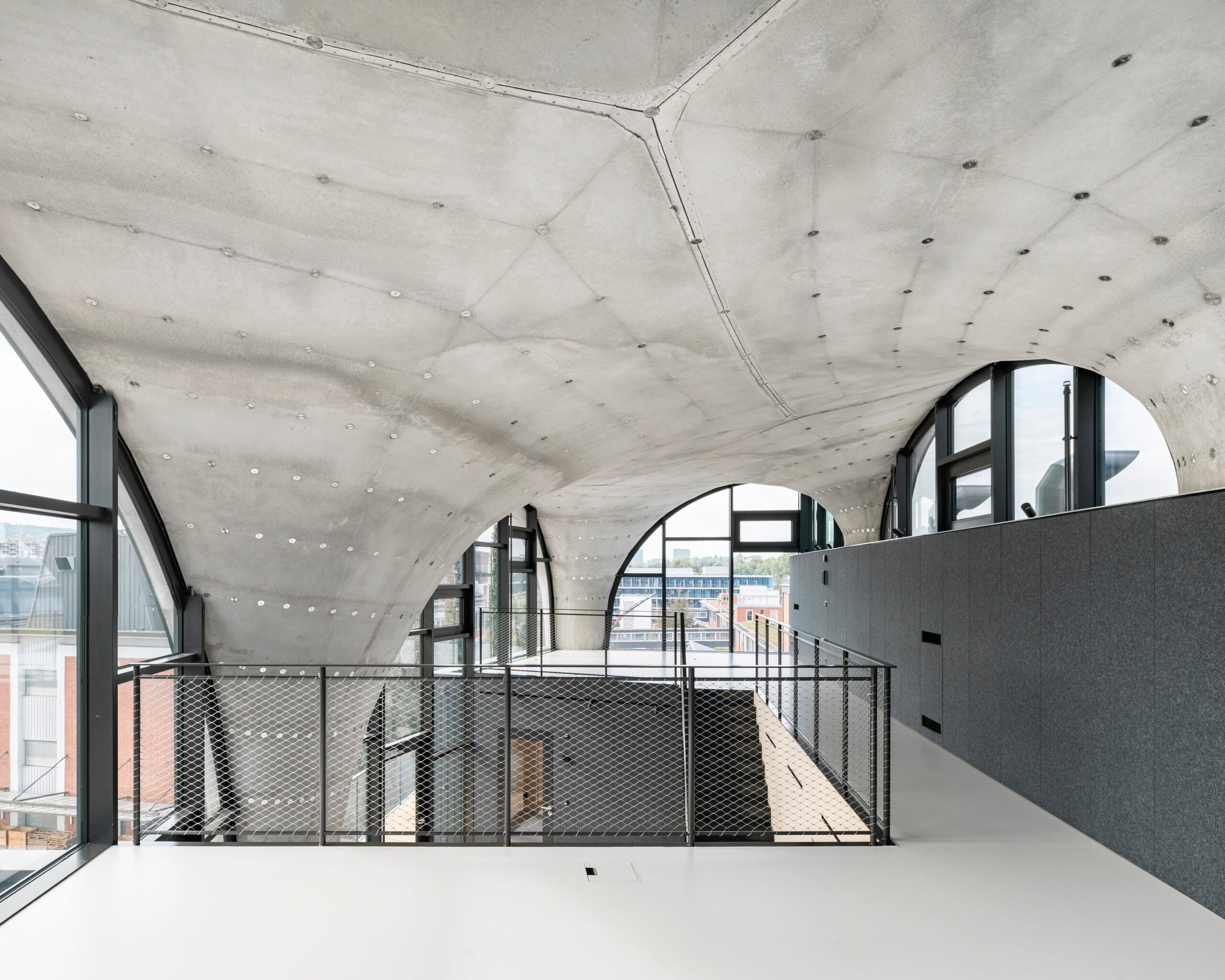
The project was designed by Zurich-based ROK Architekten in collaboration with ETH Zürich’s Block Research Group and Architecture and Building Systems research group “Ancient master builders did not have materials like reinforced concrete at their disposal and were, therefore, forced to restrict their designs to those that were buildable with more humble materials available at the time. This resulted in the use of the typical structural typologies that we know well from those times, such as domes and arches,” notes Dr. Tom Van Mele, Block Research Group senior scientist. “With the HiLo floors, we bring back these curved geometries to span space more efficiently, with much less material and with lower-strength materials, all while keeping the materials separated so they can be easily recycled at end of life. Digital fabrication technologies provide a way to fabricate and construct these curved geometries compared to more traditional floor plate solutions.”
Construction began in September 2019 with the completion of the formwork system, though colder than expected temperatures that winter pushed the concreting to Fall 2020. The medieval building techniques are largely manifested through the structure’s geometry. The roof was shaped by a flexible formwork system that deploys a cable net tensioned within the boundary frame as the primary load bearing element and a tensioned membrane acts as a shuttering layer. That same cable net is stiffened through a doubly curved geometry that deforms into its final shape under the weight of the sprayed wet concrete.
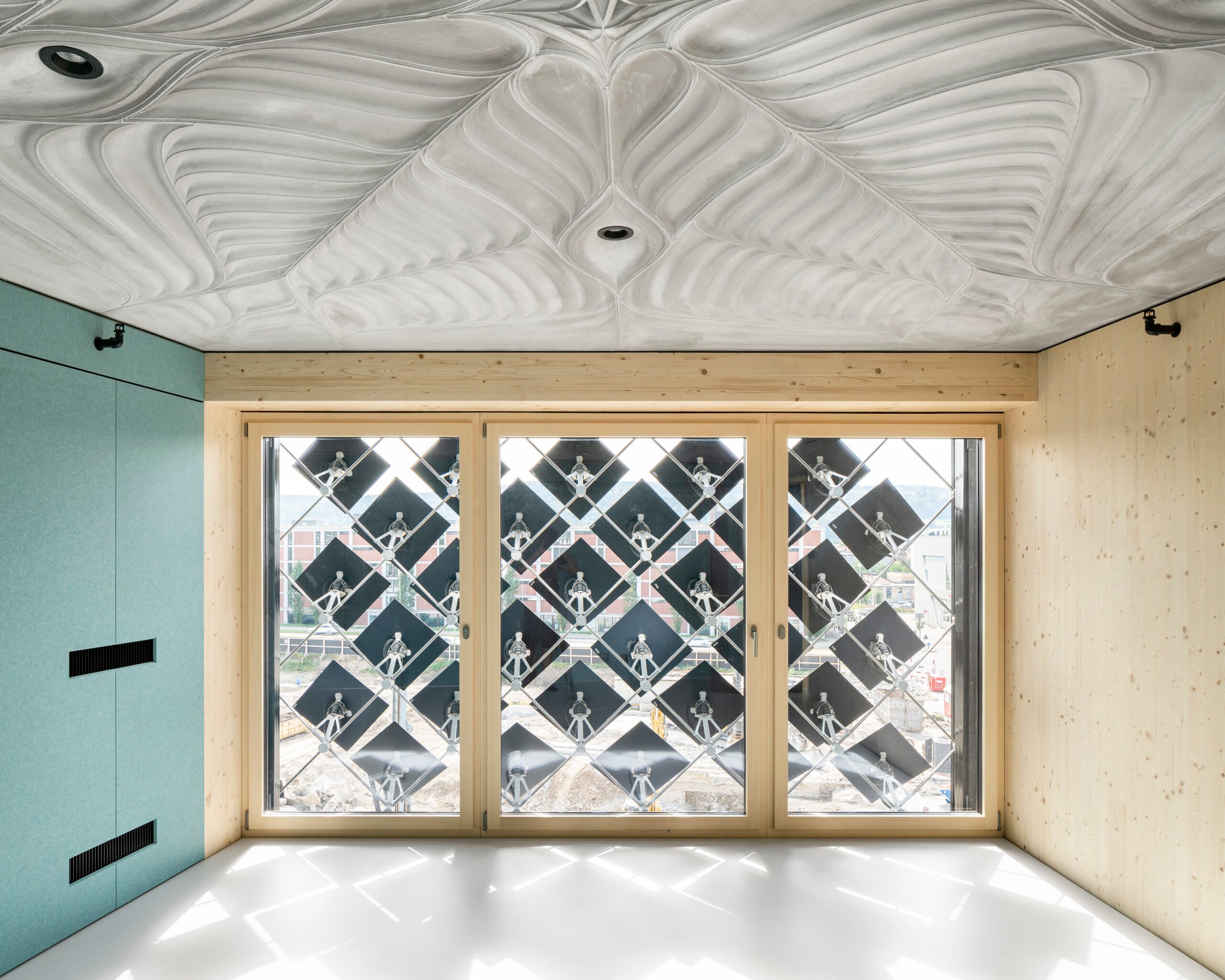
“All of the key details of the roof structure and its formwork system were worked out through prototyping in collaboration with experts and partners from industry. The principles of the developed solutions were integrated into a flexible design-to-fabrication workflow implemented with COMPAS, the open-source computational framework for research and collaboration in Architecture Engineering and Construction,” details ETH Zürich in a press release. “This workflow served as a central hub for the computational development, coordination, and planning of the key innovations and provided an effective research-to-practice transfer mechanism.”
The project’s sustainability and efficiency extend beyond the roof structure. At the floorplate, the team developed a rib-stiffened funicular system that transfers loads to structure’s corners, which shaved approximately 70 percent of the concrete and 90 percent of the reinforcement steel typically applied to a reinforced concrete floor slab. The reduction of slab width also allowed for the integration of heating and cooling pipes to establish a highly efficient radiant panel thermal system. At the facade, the team also incorporated 30 flexible photovoltaic modules that can be adjusted to maximize solar energy, or to control how sunlight enters the module.
While HiLo is the eigth module of NEST, the research building will continue to evolve in the years ahead as a testing ground for building scientists, engineers, and industry partners. Let’s see what the folks at ETH Zürich come up with next.
Would you like to comment on this article? Send your thoughts to: [email protected]
Latest
Projects
MAD Architects’ FENIX is the World’s First Art Museum Dedicated to Migration
Located in Rotterdam, FENIX is also the Beijing-based firm’s first European museum project.
Products
Discover the Winners of the METROPOLISLikes 2025 Awards
This year’s product releases at NeoCon and Design Days signal a transformation in interior design.
Profiles
These Architecture Students Explore the Healing Power of Water
Design projects centered on water promote wellness, celebrate infrastructure, and reconnect communities with their environment.