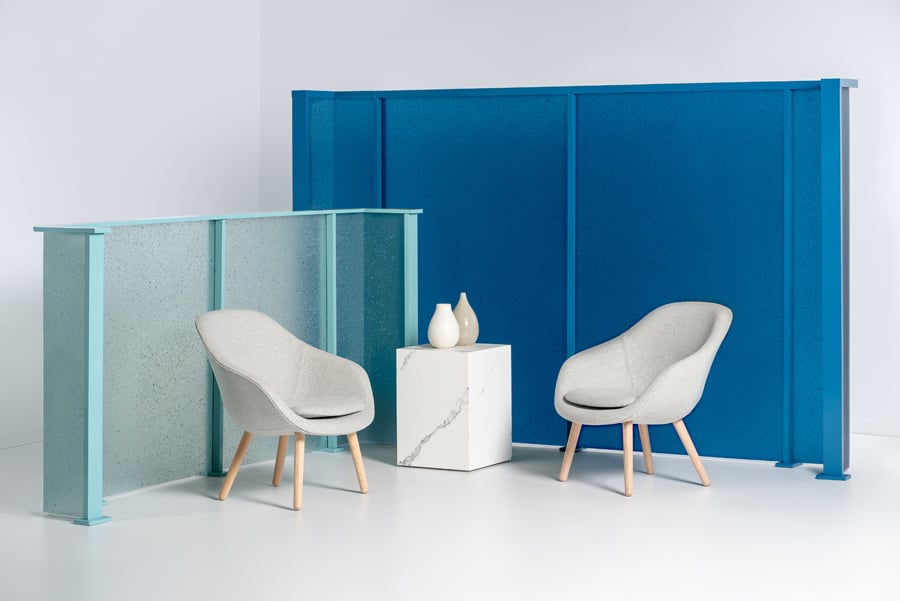
March 17, 2020
3form Doubles Down on Sustainability with Align
A new collaboration across the 3form family of companies finds eco-friendly synergies between brands including 3form, LightArt, EFI, and Springboard.
Sponsored by:
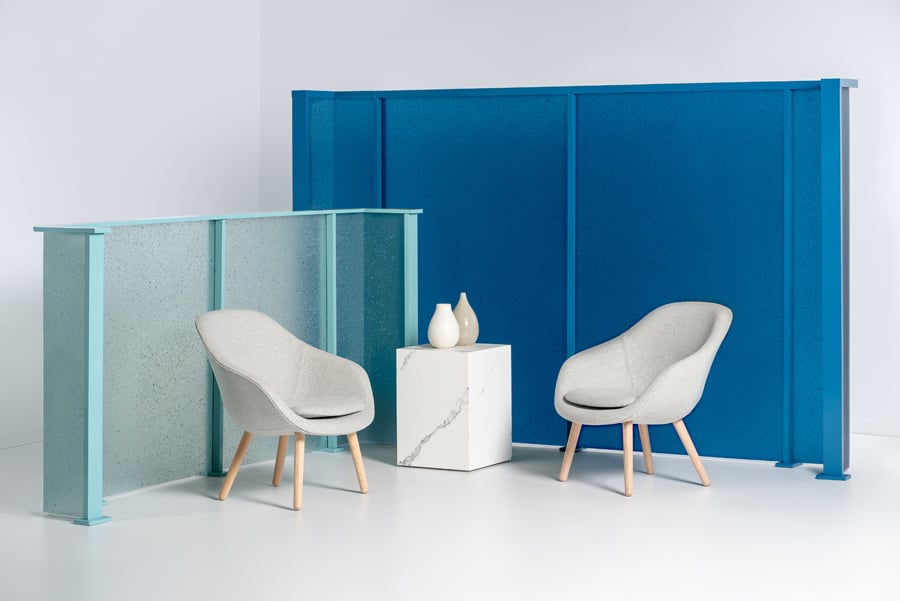
Align, a collaborative effort from the 3form family of companies, which includes 3form, LightArt, EFI, and Springboard, is synchronizing all the brands’ sustainability programs, and helping them make improvements at the product and corporate levels. 3form, a leading manufacturer of material solutions, and LightArt, a lighting fabrication and design studio, along with their sister companies are a part of an industry that is gaining awareness of its environmental costs and taking steps not only to reduce their footprint, but to create a positive impact.
“It became clear that across the industry our clients were asking ‘what are you doing for sustainability and product transparency?’” says Mike Johnson, director of sustainability at 3form. The company decided it needed to build a new framework to coordinate its sustainability efforts across its brands, that program evolved into Align. Johnson explains, “Align is a holistic lens through which we operate now, making sure that we are aware of the true footprint of our existence.” The new initiative is also the central point for clients interested in finding out more about the companies’ sustainable practices. “We really needed a go-to spot for clients and consumers to understand what we were working on in regard to sustainability,” says Ryan Smith, president and creative director of LightArt.
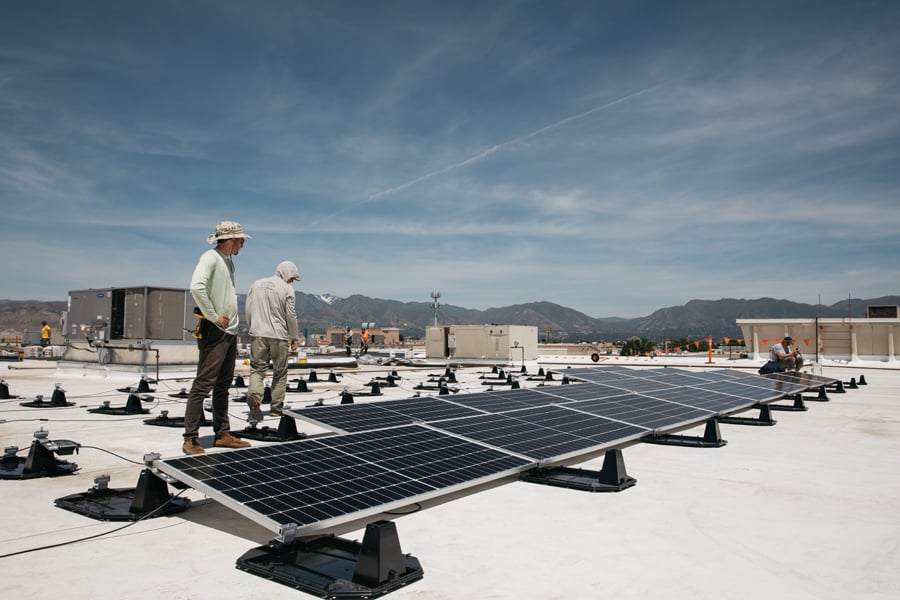
Their new modus operandi involves making commitments on a product level and on an organizational one. At the product level, they are pursuing the Living Product Challenge, a framework for manufacturers to create products that are healthy and free of toxins, ethically manufactured, and net-positive for the planet. “We are trying to be net positive for the environment, not just net-zero,” says Johnson.
Align has brought the brands together to take a closer look at the raw materials and supply chains that make their products possible. At LightArt they dug into their component parts like the cords, plugs, and wires that go into every product. “We needed to find products that were the same quality, but didn’t have any of the toxins, dangerous plastics, or excess materials we saw in the industry standard,” says Smith. Now, over 90 percent of their components are manufactured in the United States, where they can be sure of quality, as well as environmental and labor standards.
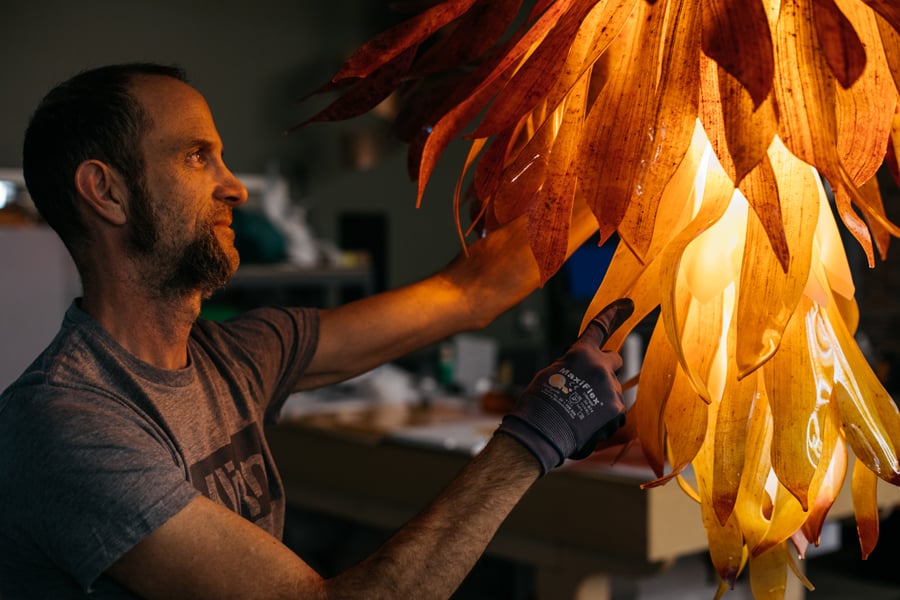
For 3form, it was essential that their Varia panels use the greenest chemistry possible, without sacrificing performance, says Johnson. They are also looking at social equity and impact. “Can we make a difference in developing countries by providing better wages to our artisans and suppliers, not supporting slavery or using conflict minerals?” asks Johnson. Through socially conscious manufacturing, as well as a whole slew of sustainability programs, everything from solar panels to encouraging employees to bike to work, 3form is aiming to have a net-positive impact.
At the product level, 3form redeveloped their signature Varia line of translucent materials. Life-cycle analysis showed that while the product contains 40 percent pre-consumer recycled materials, there was an opportunity for improvement. “The biggest issue was coming from waste in the manufacturing process, i.e. trimmings,” said Johnson. “We re-tooled our factory to reduce trimmings by 2.5 percent per sheet. Across millions of sheets of Varia resin, that adds up.” The remaining trim waste became Flek, a product made of approximately 75 percent recycled materials and an indication of what might be in store for Align as the companies continue to find sustainability synergies across both brands.
“The goal of Align,” says Johnson, “is to make sure that we are all operating from the same standpoint, understanding the same climate crisis, and moving forward in the same direction.”