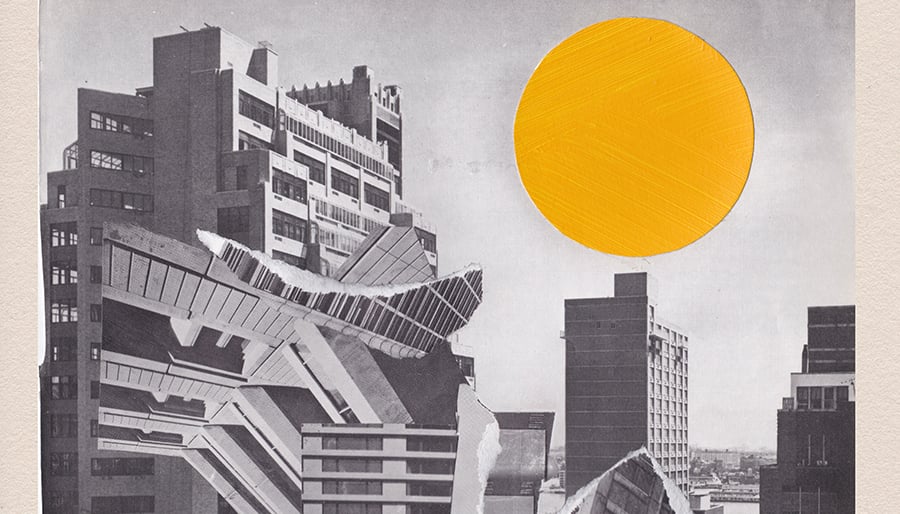
January 30, 2019
When a Building Comes Down, Where Do It’s Materials Go?
Recycling five essential materials—steel, concrete, drywall, glass, flooring—turns up different challenges, but architects can be part of the solution.
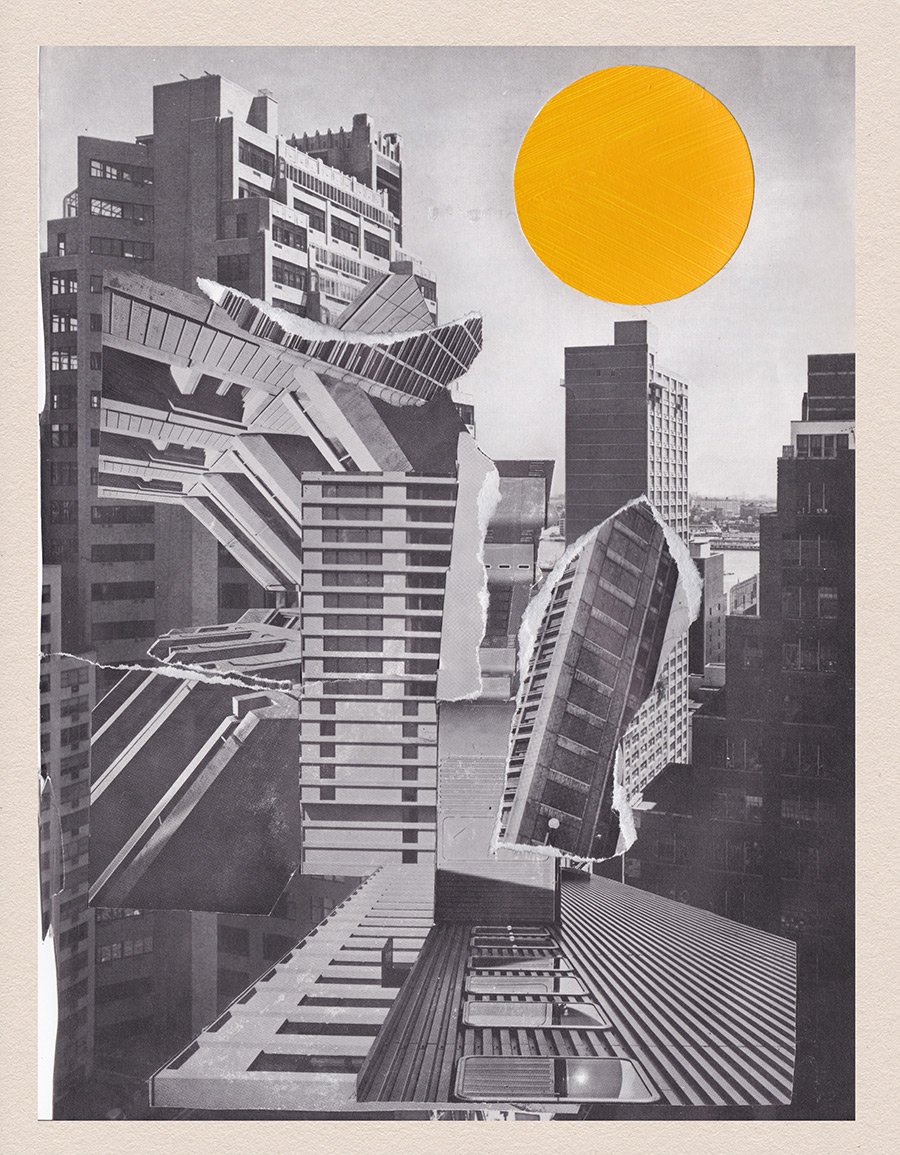
To understand buildings, consider cities. They are evolving, iterative systems whose peripheries and hinterlands are implicated in their growth, demanding material flows of natural resources and the expenditure of energy. So too with buildings, although such thinking is relatively new. And, as urban development marches on, it is as important to analyze the embodied energy and material output of buildings when they come down as when they go up. Such flows are sometimes redirected into recycled building products, but more often they terminate in landfills, waterways, or worse.
As the environmental crisis worsens, we must ask: Can we reduce our demand on new resources? Need our built environment be in perpetual flux, an endless succession of destruction and rebuilding? For Kiel Moe, professor of architecture at McGill University, the discourse surrounding demolition and recycling is “fundamental to an ethos of planned obsolescence” and isn’t “a viable way to think about sustainable construction.” Resisting this “cycle of buildings” assigns greater importance to the architectural imagination— something that should excite designers. Creative reuse, retrofitting, and, most importantly, designing programmatically versatile buildings that last should be architects’ main objectives.
But the demolition-construction cycle also entails pragmatic challenges, which may offer important—albeit fundamentally incremental—solutions to our waste predicament. Design for disassembly should become part of architectural practice, and planning to systematically sort materials during demolition can make it easier to repurpose them. The high environmental and logistical cost of removal, transportation, and processing of building materials for recycling should also give pause to wrecking-ball zealots.
Ultimately, once building materials are untethered to a structure, they will find a new home, preferably in an up-, re-, or downcycled context. Here, we review the end-of-life potential of five major construction elements: steel, glass, concrete, drywall, and flooring. While varying in impact and availability, such examples point a way forward to mitigating the environmental costs of demolition, and toward closing the loop on circular design, specification, and development.
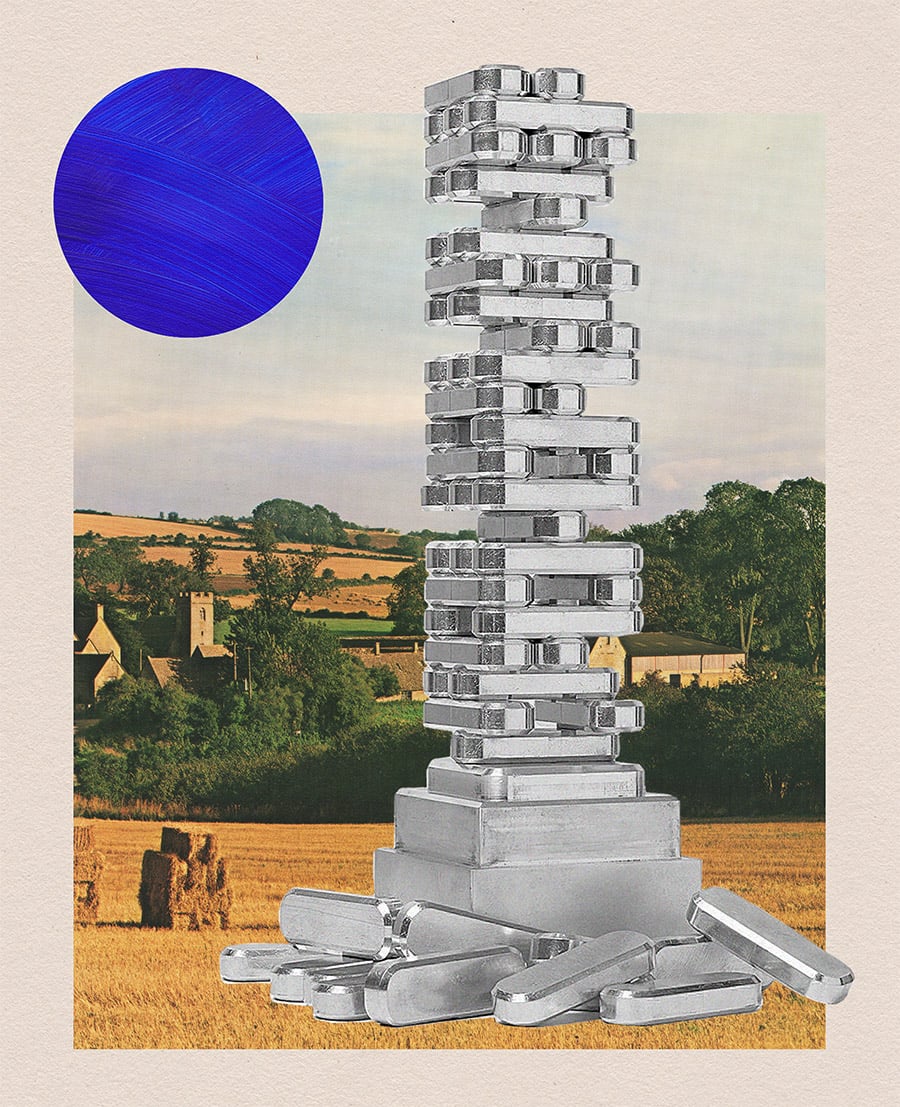
Steel
Steel is the most common structural framing material for nonresidential buildings in the United States and offers an ideal example of a recycling flow that approaches circularity. After a building is demolished, “pretty much all steel will get recycled,” says Moe. In fact, steel is the most recycled construction material in the world, with about 98 percent of structural steel avoiding landfills.
This is due in large part to the nature of steel production itself, which relies largely on melting down preexisting steel, and to the economic conditions of supply chains that incentivize its reuse. Other metals (including aluminum) are also frequently reintroduced into the production cycle in what Moe calls “a pretty standard flow” in the current construction context. For example, steel made from scrap—sourced as postconsumer material or as a by-product of manufacturing—saves iron, coal, and limestone (not to mention carbon emissions) relative to steel production from virgin materials.
The picture is less impressive for steel used as rebar and as reinforcing material in concrete construction: Only 71 percent of such steel is recycled, according to the Steel Recycling Institute. The lower percentage indicates the importance of neatly separating different materials during demolition to better guarantee their efficient reuse. Although sorting out multi-material building elements is difficult, it can lead to safer repurposing.
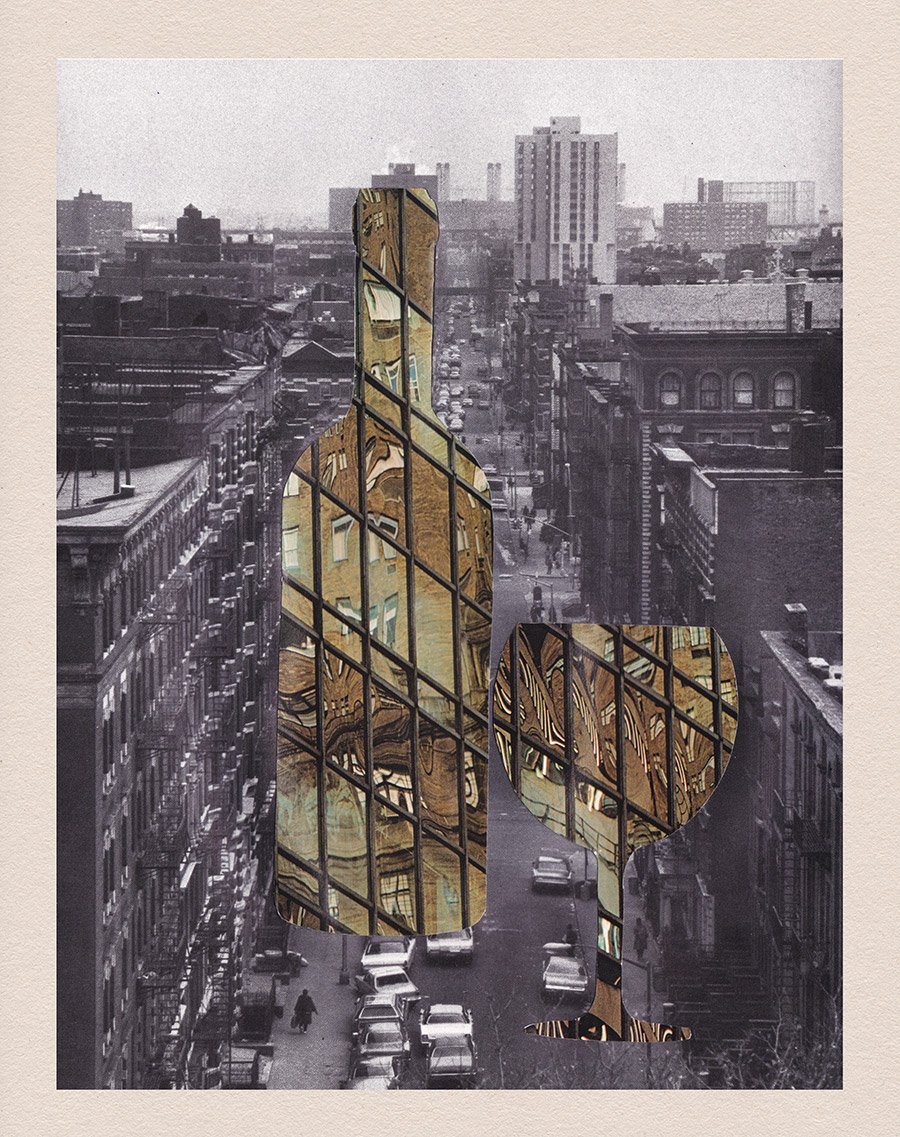
Glass
Architectural glass is among the most salient building products in use today, used decoratively throughout interiors and deployed in the envelopes of supertall and “transparent” structures. Once removed from its built context, glass is, in theory, a surprisingly reusable material—infinitely recyclable to virgin quality—but several important caveats qualify its broad capacity for recycling. The main obstacle is ensuring glass panels are not mixed in with other refuse during demolition. Another, according to Sydney Mainster, a designer and director of sustainability at the Durst Organization— which owns about 16 million square feet of commercial and residential space in New York—relates to the widespread coloration of glass. “You can make clear glass into new products quite easily,” she says, “but colored glass is almost always landfill.” Mainster attributes this to the lack of end-user demand for mixed-color recycled glass products: The market just isn’t there.
Mic Patterson, a designer who has researched and written extensively on sustainability and architecture, says several glass treatments and surface techniques also preclude opportunities for recycling building materials. In many cases, processes meant to improve glass envelope performance— such as heat treatment, lamination, coating, and double- and triple-pane insulation—“render the primary fl at glass material unsuitable for recycling.” In these cases, he says, the raw material, as well as its embedded engineering know-how and production, becomes unusable. “In focusing on thermal performance,” he adds, “we have entirely neglected important attributes of durability, reuse, and recyclability.”
If all else fails, high-performance glass can be downcycled as aggregate in lieu of pea gravel and stone. In this manner, glass is finding its way into mixes for interior uses like ceramic countertops and in concrete, although it is unclear whether such cement-glass mixes perform as well technically.
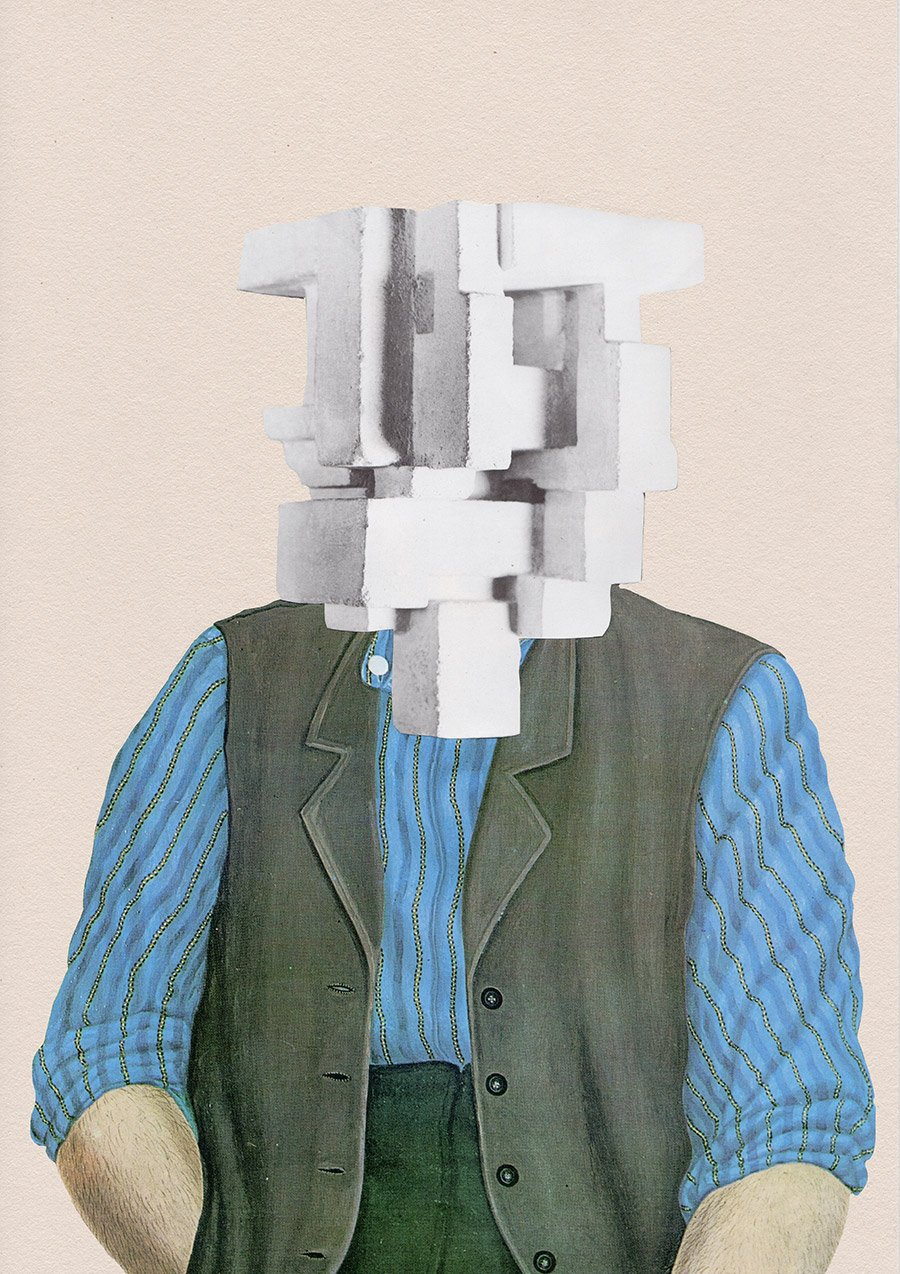
Concrete
Concrete is critical in laying foundations, delineating floors and walls, and reinforcing building elements, but its compositional ingredients of cement and aggregate are not renewable. (Sand, for example, concrete’s most common aggregate, is being harvested to near exhaustion.)
There are at least two major barriers to recycling concrete. Like many building products slated for reuse or recycling, concrete faces the challenge of isolating its core materials. Installed concrete is never just concrete, but is paired with everything from mortar paste and gypsum to trace plastics, metals, and woods, says Blaine Brownell, an architect and editor of the Transmaterial book series: “The main difficulty concerns the various contaminants that are often found in demolition waste.” Concrete’s increasingly common chemical additives also reduce its recyclability, according to Dirk Hebel, professor of sustainable construction at the Karlsruhe Institute of Technology, since unwanted and potentially hazardous composites should not be recycled into new products. For these reasons, says Hebel, “usually when we talk about concrete recycling, we talk of downcycling processes.”
The most common downcycling use is of shredded or pebbled concrete as aggregate, or filler in roadbed construction, retaining walls, and earthworks. Brownell cautions, however, that such infrastructural repurposings are not as simple as they sound. Using different aggregates can be “tricky,” he says, “and the process must be carefully managed to ensure the desired mechanical performance.” Hebel adds that “only certain percentages [of concrete aggregate] are possible in order to keep the desired strength requirement.”
Brownell and Hebel agree that architects and designers can be a part of the solution. By taking steps to ensure building materials are cleanly sorted after a demolition and by working with engineers and contractors to specify recycled-content concrete in projects, they can help reduce the volume of concrete entering our waste stream and develop the basis of a circular construction model.
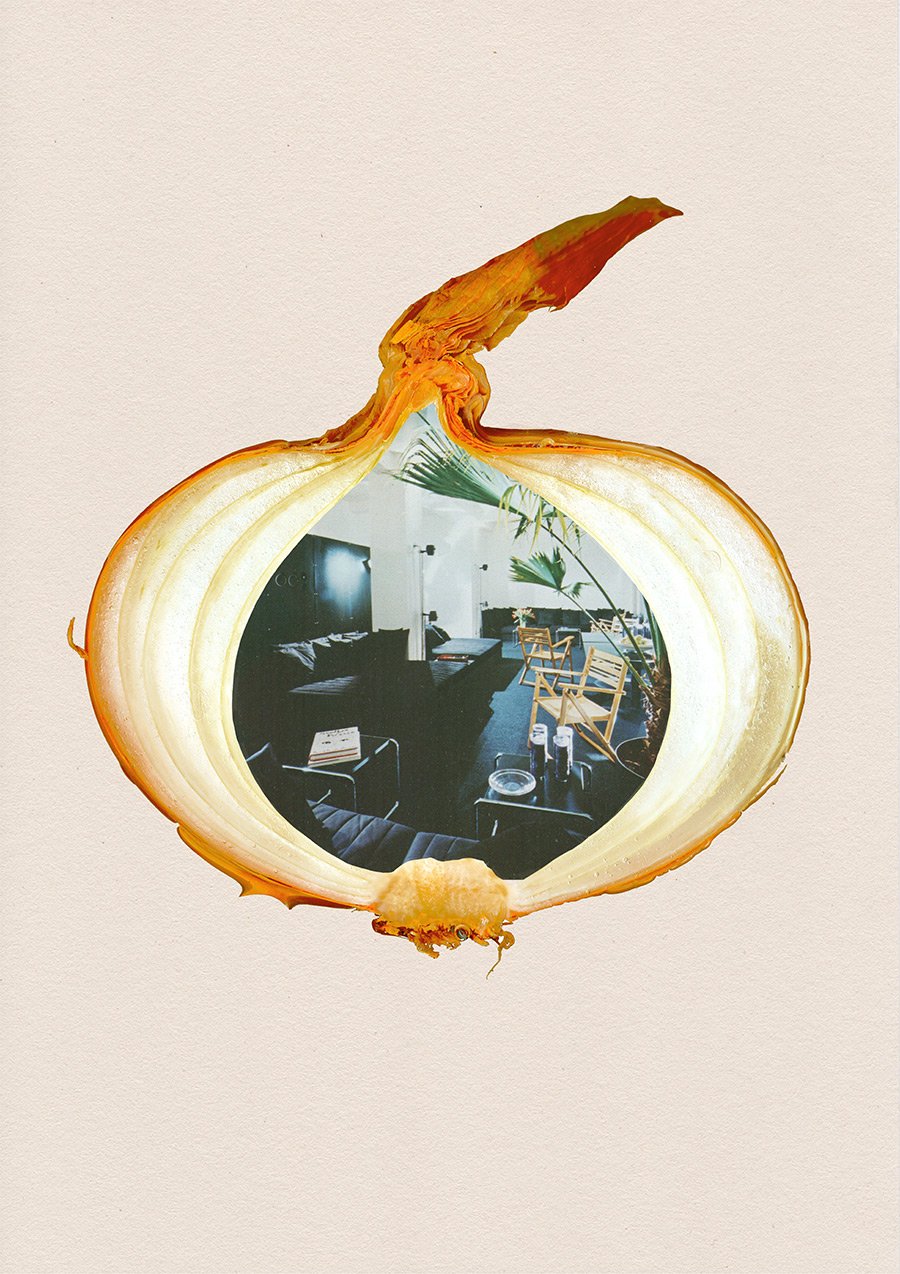
Drywall
Drywall (also known as gypsum board) constitutes nearly all walls, plus some ceilings, in commercial builds. At least in theory, it is an extremely recyclable building material, provided its layers are kept intact. “Drywall is two pieces of paper and then that gypsum core,” says Mainster, of the Durst Organization. “You want to keep it as whole as possible.”
Drywall’s paper envelope can be ground down and recycled like any paper or wood product, and the gypsum core can be infinitely recycled without any significant loss of performance. “This is the idealized closed-loop wallboard manufacturing cycle,” Mainster sums up—provided there is foresight in planning the material’s removal. (Packer trucks and mixed-refuse Dumpsters, commonly used in demolition, are out of the question, since they don’t keep the drywall whole.)
Key goals in building with drywall, according to Mainster, should be minimizing the use of virgin-mined gypsum and avoiding synthetic gypsum, which is a by-product of coal-fired power plants and may be toxic because of its heavy-metal content. Legislation may hold the key to advancing drywall recycling, but statutes vary throughout the country. Especially stringent laws prescribing reuse and prohibiting landfill disposal in Boston and in the Pacific Northwest—a similar proposal is currently under consideration in New York City—have resulted in notably high rates of drywall recycling.
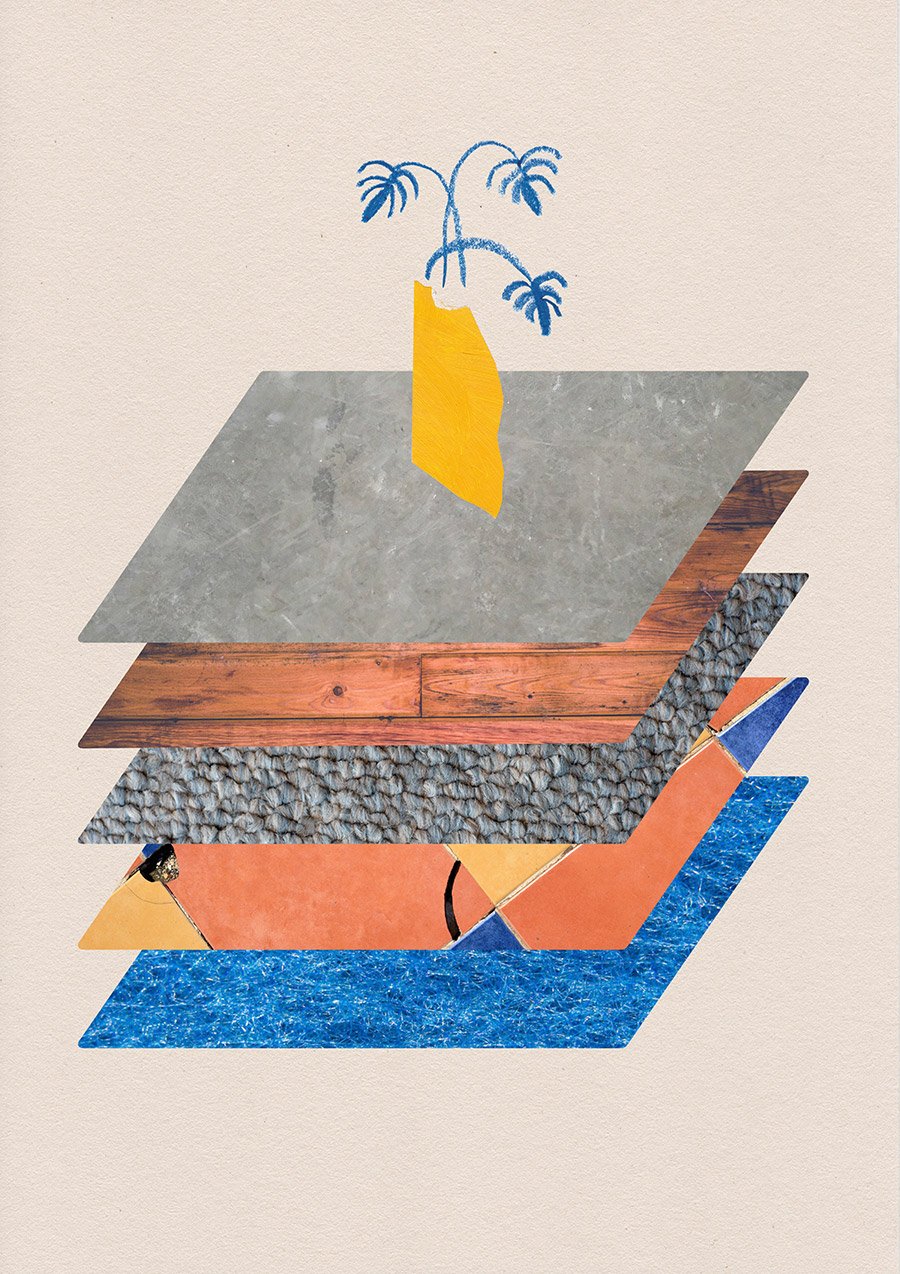
Flooring
Carpet tiles and PVC, vinyl, and resilient surfaces predominate in commercial flooring, and each comes with its own recycling challenges. Less than 10 percent of carpeting is recycled, and the central obstacle lies in the materials required to install tiles—such as adhesives, latex and calcium carbonate backing, and polyurethane cushions. A range of manufacturers, such as Shaw, Interface, and Tandus Centiva, have rolled out reclamation and takeback programs, meeting with considerable success in diverting flooring waste from landfills, but they are the exception that proves the rule.
Sean Ragiel, president and founder of CarpetCycle—a New Jersey–based company that aims to find uses for postconsumer carpet and building products—stresses the importance of removing carpet tiles as cleanly as possible. This is as much an economic calculation as a material one: Backings are low-value components that contaminate higher-value plastics like nylon and polypropylene; when components are jumbled, “the materials are essentially ruined,” says Ragiel. Absent legislation and economic incentives, the best last resort, Ragiel says, is to use shredded broadloom carpets as a coal substitute in cement kilns, a technique common in Europe.
For hard-surface flooring, the state of PVC recycling is also mixed. Despite successful recycling initiatives by manufacturers, “the economics of cheap plastics production have been a powerful counterweight,” says Jim Vallette, research director of the Healthy Building Network. In addition, despite pushes toward material transparency, toxic ingredients are still prevalent in luxury vinyl tiles and PVCs, foreclosing the recyclability of those surfaces. Adhesives, insulation, and sealants also bedevil recycling efforts: According to Vallette, even leaders in the recycled-flooring sector can rarely offer products with more than 20 percent postconsumer content. “The next frontier is for a company to achieve true circularity,” he says. “Zerovirgin- material floors would be a real accomplishment.”
You may also enjoy “Sustainability Glossary: 6 Terms You Should Know.”