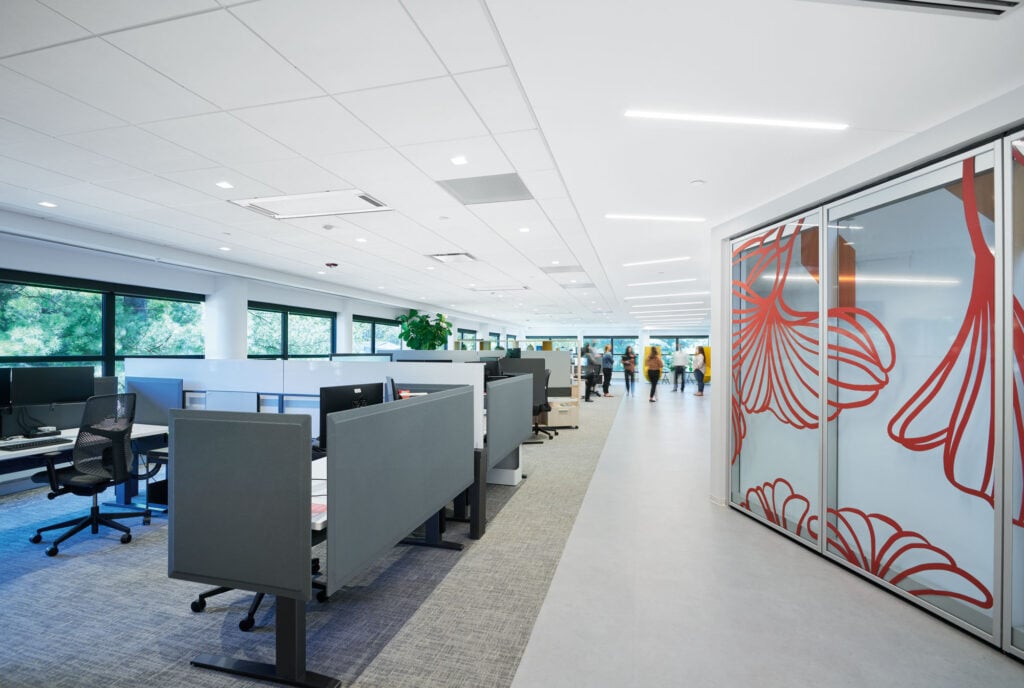
November 3, 2021
Quick Comparison

A first step to reducing embodied carbon in the built environment is for architects to identify carbon hot spots—the materials or systems that contribute the most to a building’s embodied carbon. It is also important to consider when reviewing finishes, that over the lifetime of the building, the cumulative embodied carbon of interior renovations may surpass the emissions of both structure and envelope. The most widely accepted way to do this is through a whole-building lifecycle assessment (WBLCA), along with other tools like the Carbon Leadership Forum’s Embodied Carbon Calculator for Construction (EC3). Architects, designers, and engineers can compare materials based on a uniform understanding of their lifetime contributions to the climate crisis.
With the full picture of a product or material’s carbon costs, specifiers and interior designers can then make the best choices for the environment when selecting interior finishes as well as structural materials. Ceilings in the Armstrong SUSTAIN® portfolio, for example, are free of Red List chemicals per Living Building Challenge™ 4.0, have HPDs that say exactly what chemicals and materials are in each product, and have Environmental Product Declarations, that show the lifetime impact the product has on the environment. They also have Declare® labels, which are easy references that are sometimes called nutrition labels for building products. This wealth of information takes the uncertainty out of embodied carbon analysis, combined with an evaluation of material health, both allowing designers to make smarter choices more easily. Reducing the carbon footprint of the built environment is a massive undertaking, but the specification choices designers make add up, making a difference in decarbonizing the built environment.
Would you like to comment on this article? Send your thoughts to: [email protected]
- No tags selected
Latest
Projects
Monroe Street Abbey Is an Armature from the Past for the Future
Discover how Jones Studio transformed the ruins of a former Baptist church in Phoenix into a community-centered garden and event venue.
Profiles
Breland–Harper Mines the Past to Design a Better Future
In less than a decade, Ireland-Harper, the Los Angeles–based studio has completed over 100 adaptive reuse projects.
Products
How the Furniture Industry is Stepping Up on Circularity
Responding to new studies on the environmental impact of furniture, manufacturers, dealers, and start-ups are accelerating their carbon and circularity initiatives.