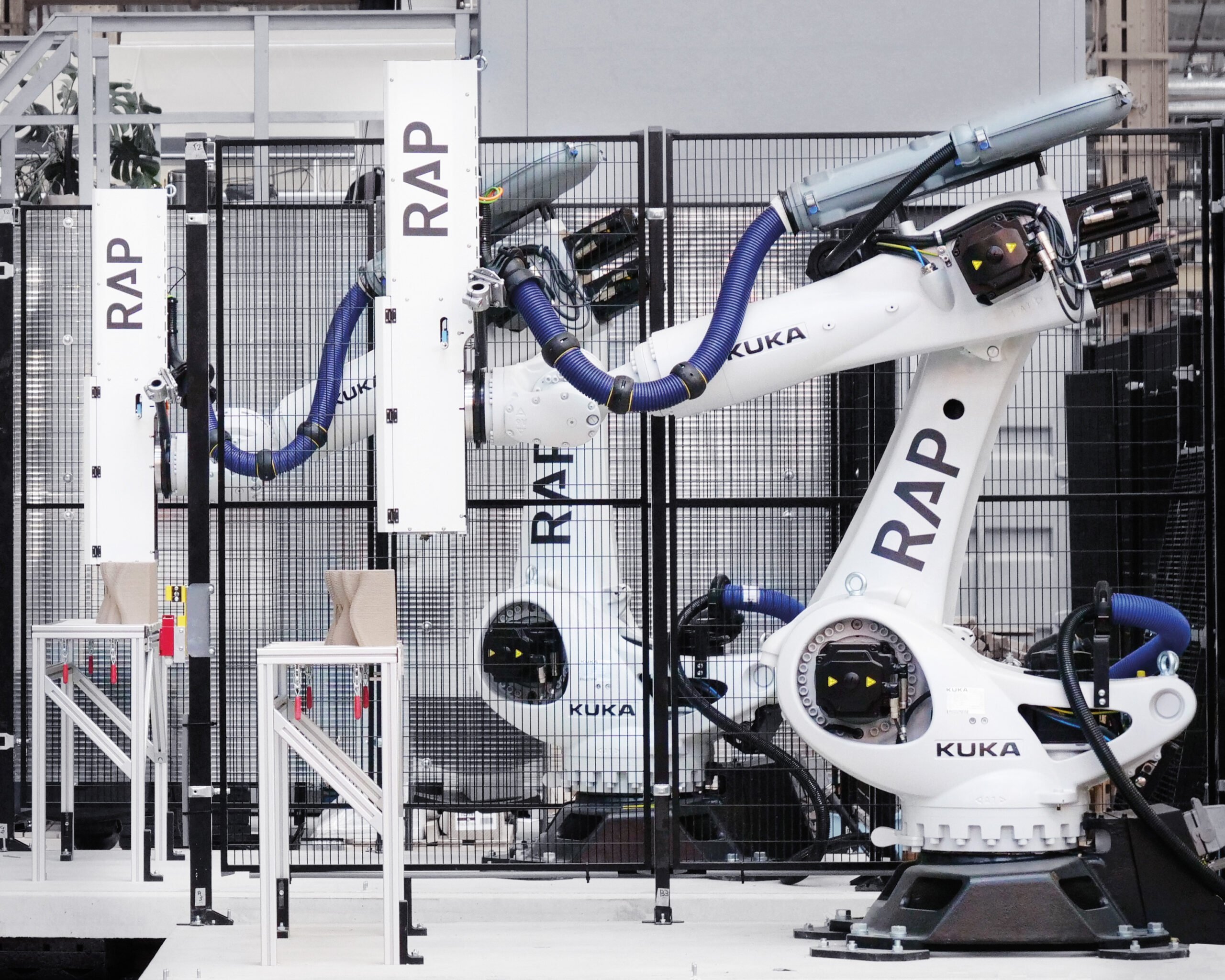
June 27, 2024
An Architecture Office of the Future
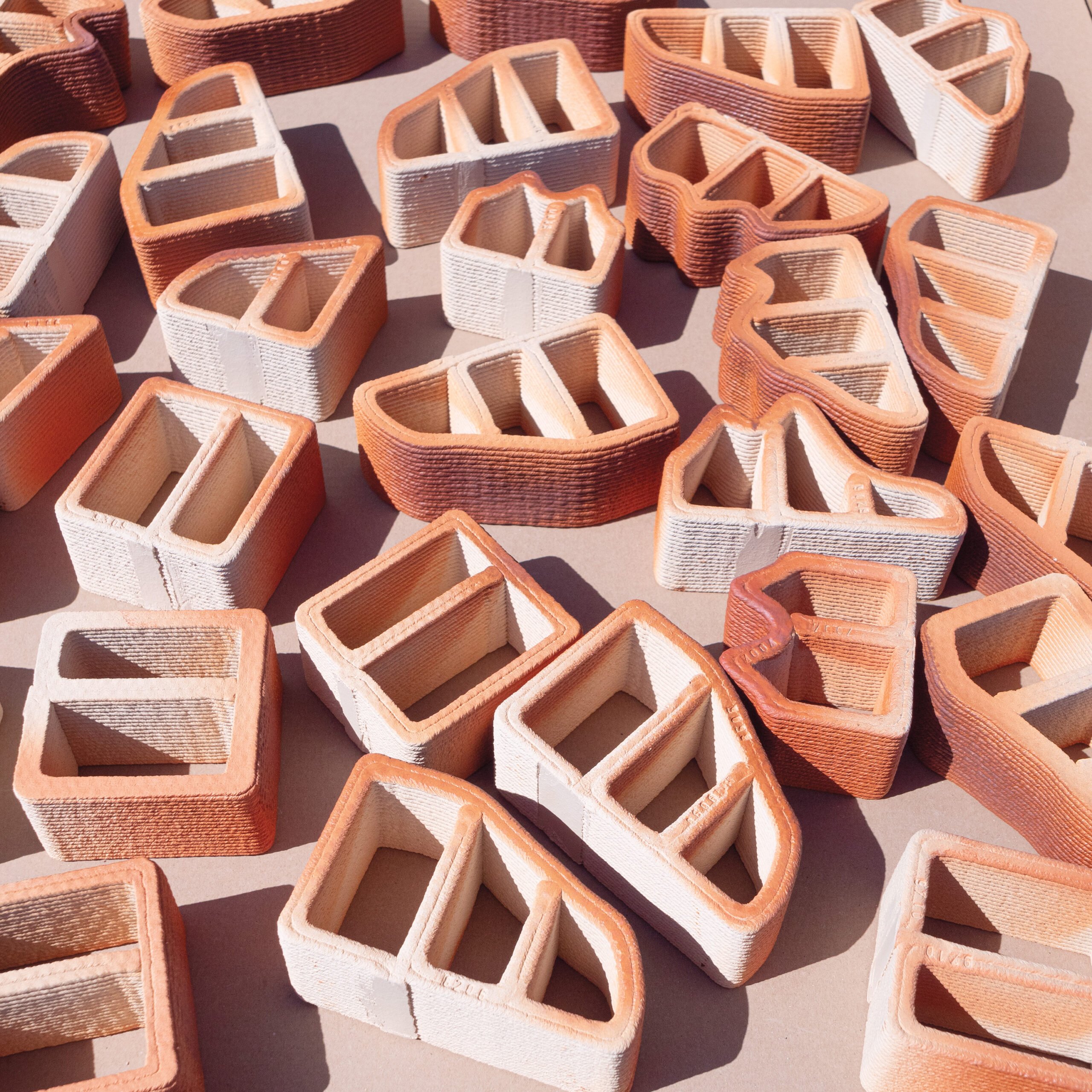

In 2020 the studio shaped the acoustic walls for the main auditorium of Rotterdam’s new Theater Zuidplein, using their parametric design skills to shape 6,000 aluminum panels painted in a bright red (the same color as the auditorium chairs).
A few years later the firm received international attention for New Delft Blue and Ceramics house, two projects that make use of innovative 3D-printed ceramic tiles. In Delft the studio got the commission to upgrade two gateways leading into the large inner courtyard of a newly built, rather conventional housing block. “We had absolutely no experience with clay or ceramics,” says ter Hall. But the city of Delft is known worldwide for its specific tin-glazed earthenware that has been produced in the region since the 1600s, otherwise known as delftware or delft blue. Connecting to this tradition, Studio RAP developed an algorithm that generated a 3D leaf pattern for both gateways in the iconic hue, and translated it into 3,000 ceramic panels.
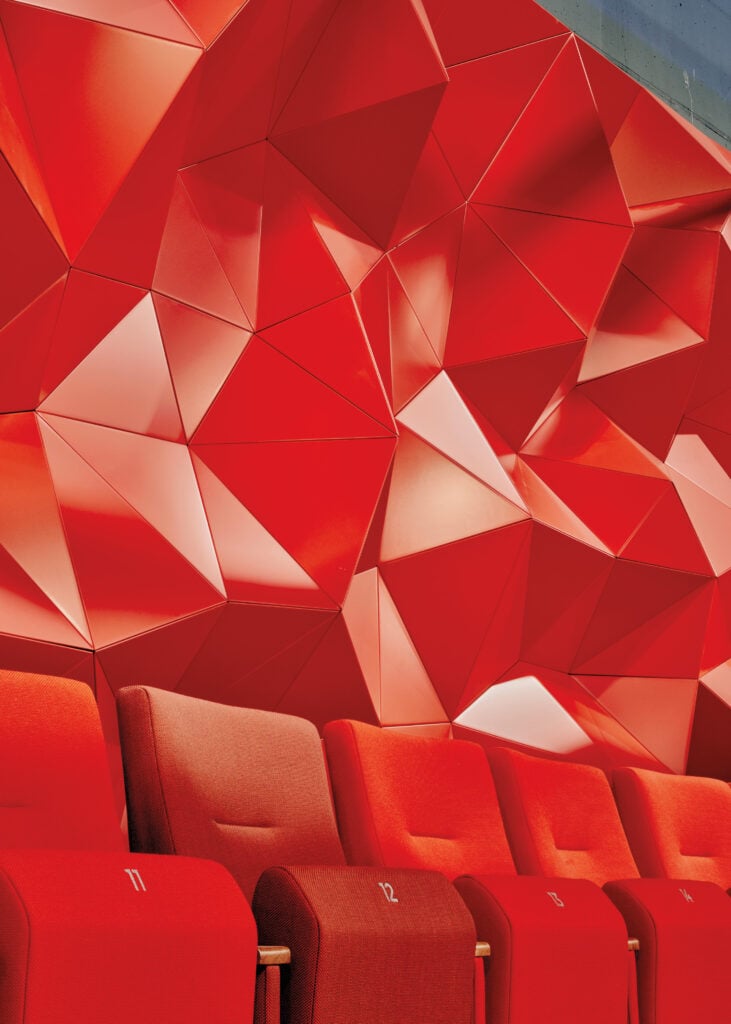
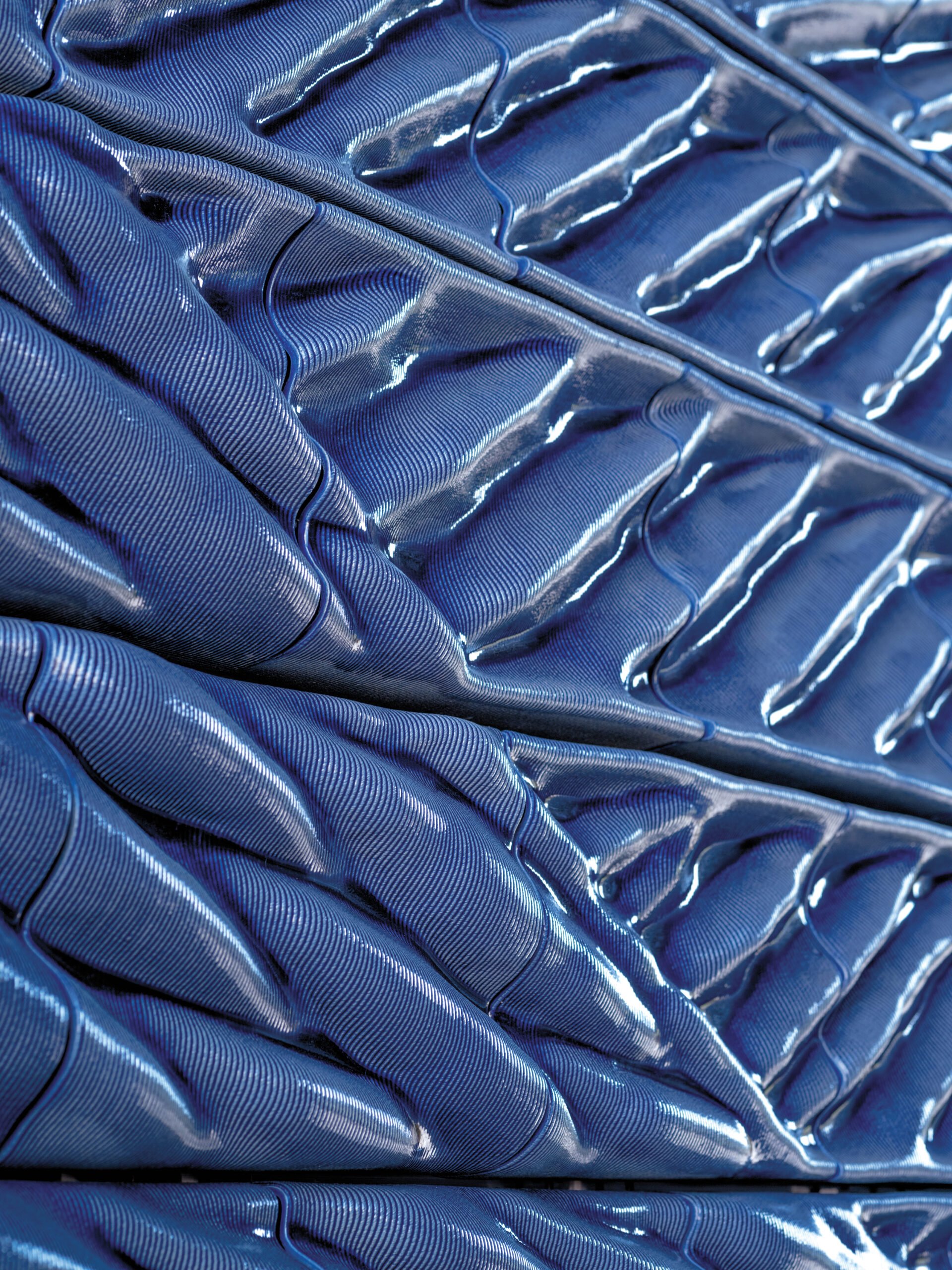
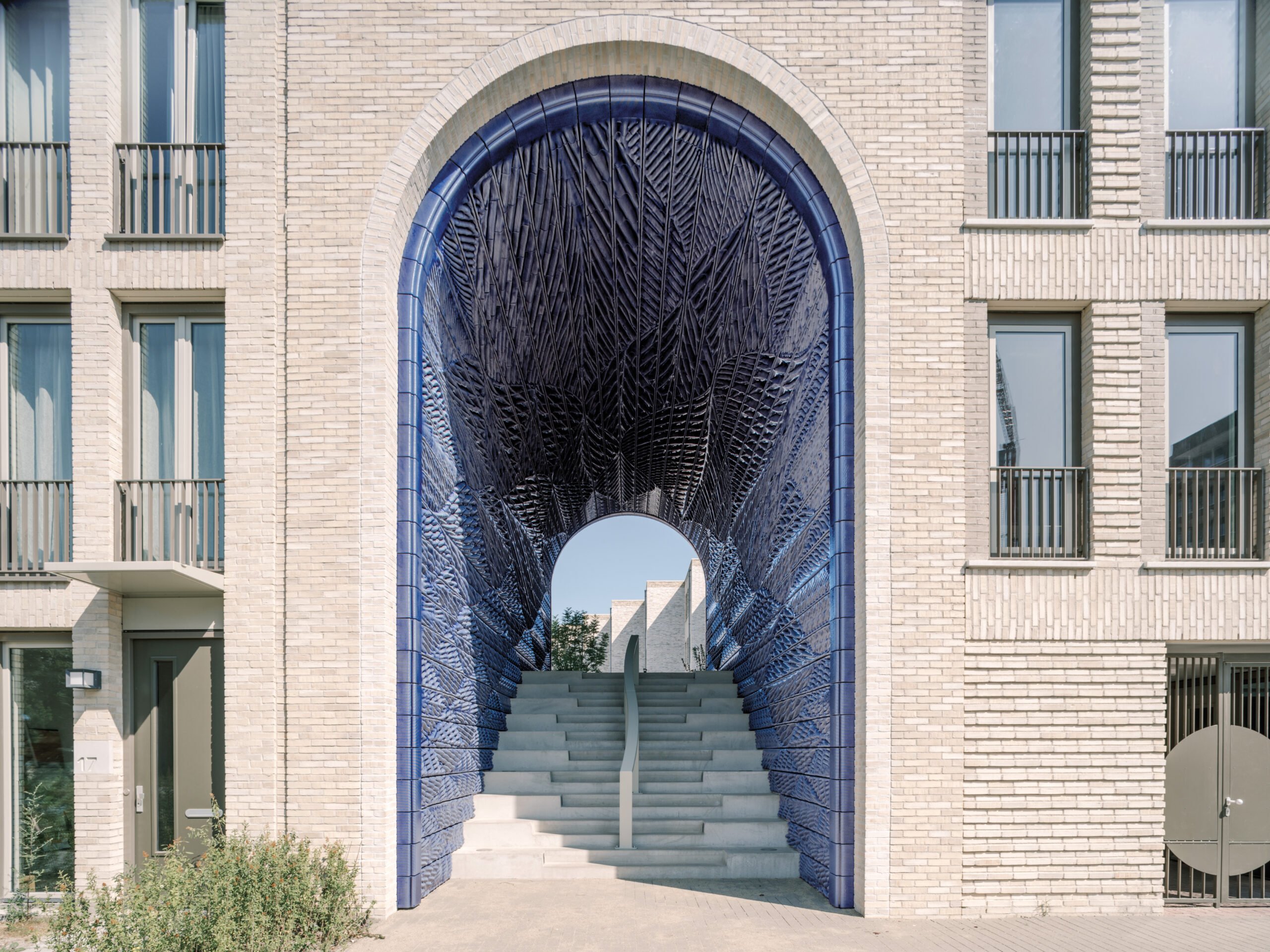
The other project is located on one of Amsterdam’s busiest shopping streets, where they clad the facade of a future commercial space with a new structure of three-dimensional tiles that “echo the tripartite order of the old brick facades in the neighborhood,” explains ter Hall. “But we also took inspiration from the structures of knitwear.” So ter Hall and van Beerendonk found themselves analyzing stitch patterns, interwoven yarns, and creases, translating these lightweight structures into fired ceramics.
To produce both projects, Studio RAP collaborated with a centuries-old, traditional producer of Dutch ceramics, Royal Tichelaar. Ter Hall and van Beerendonk set up 2 one-armed robots directly in the factory. “As the hollow clay forms are very fragile before they are fired,” says ter Hall, “it was easier to place the robots directly near the large [kilns] instead of transporting the clay.”
In a fully digital design process, the architects send their codes to the robots, which print the clay forms. These are then fired and glazed by Royal Tichelaar before being sent to the architects for testing. “It took us more than three years of testing and readjusting the production process again and again,” remembers ter Hall. “But I think it was worth the effort.” They are currently working on all types of projects using robotically produced prototypes made in-house. It is this combination of design studio, workshop, and factory that turns Studio RAP itself into a prototype for the architecture office of the future.
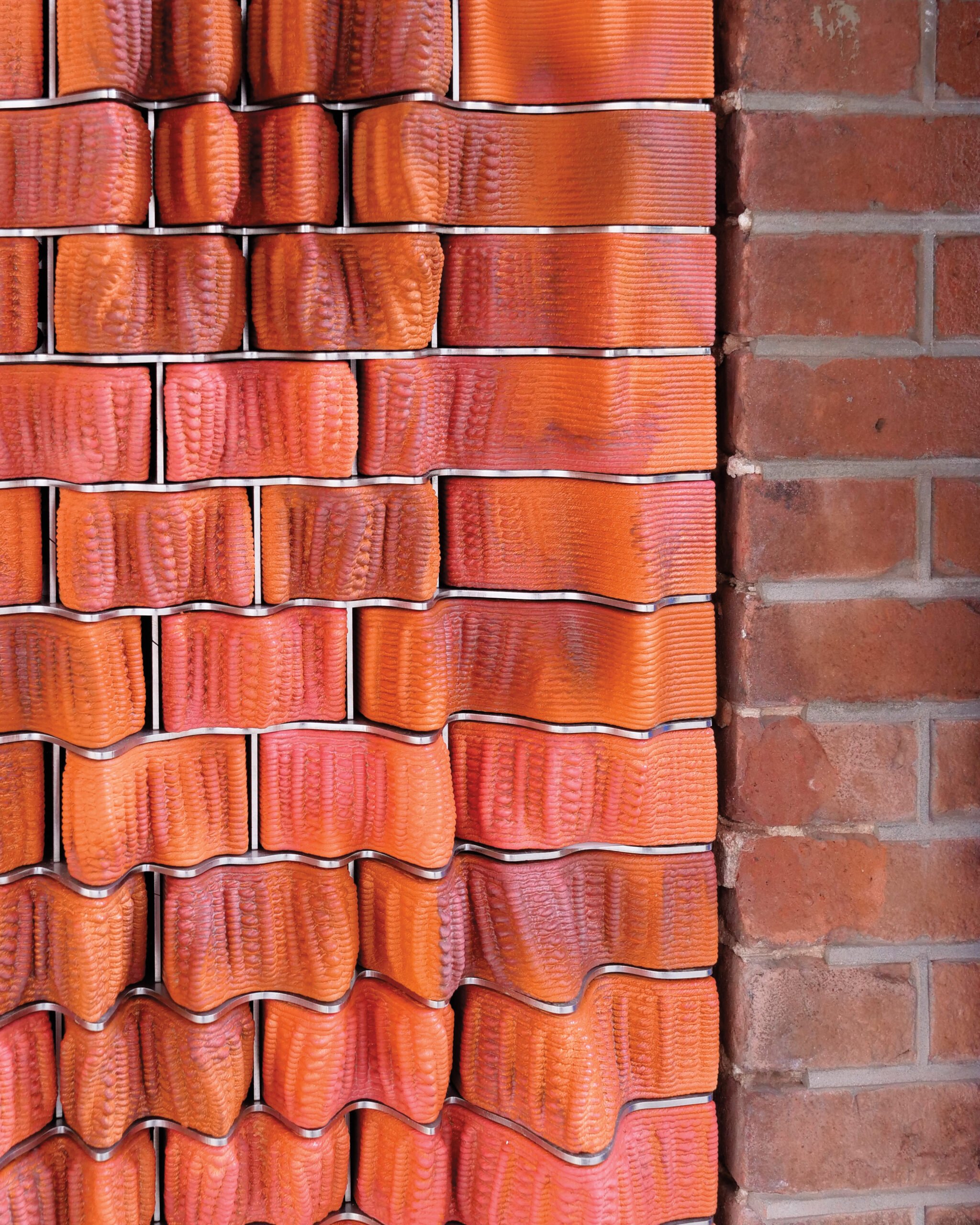
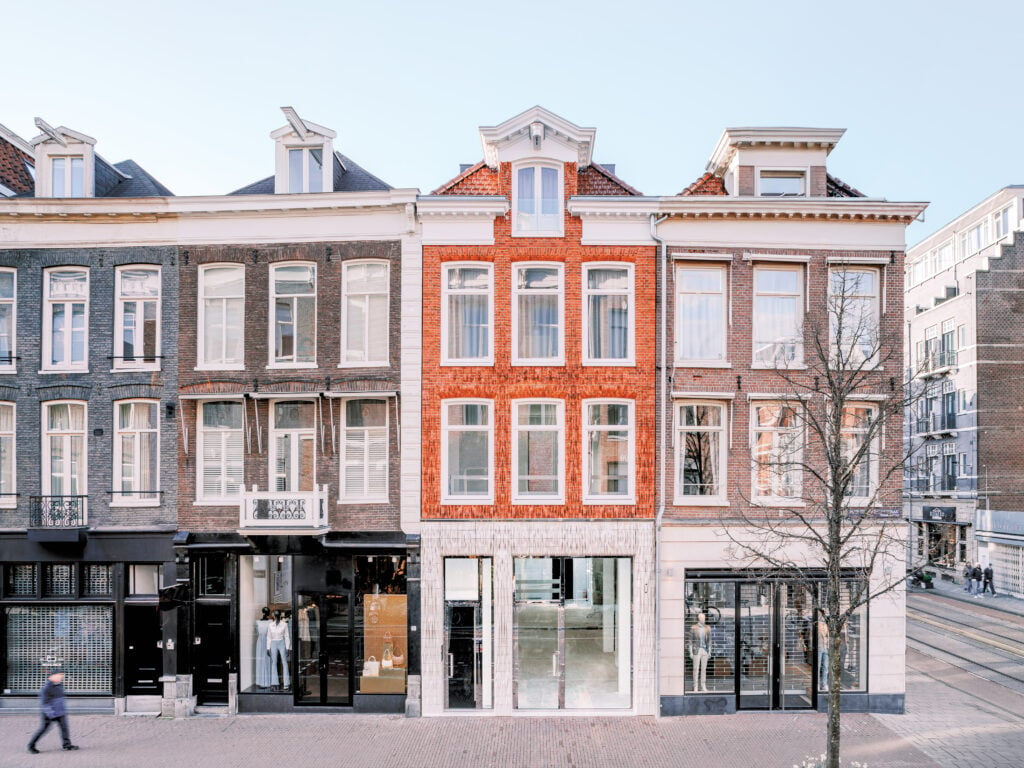
Would you like to comment on this article? Send your thoughts to: [email protected]
Related
Profiles
BLDUS Brings a ‘Farm-to-Shelter’ Approach to American Design
The Washington D.C.–based firm BLDUS is imagining a new American vernacular through natural materials and thoughtful placemaking.
Products
Discover the Winners of the METROPOLISLikes 2025 Awards
This year’s product releases at NeoCon and Design Days signal a transformation in interior design.
Products
How to Make Smart, Sustainable Surfacing Choices
Discover the latest information and offerings in this category to help you make beautiful, sustainable choices on your next project.