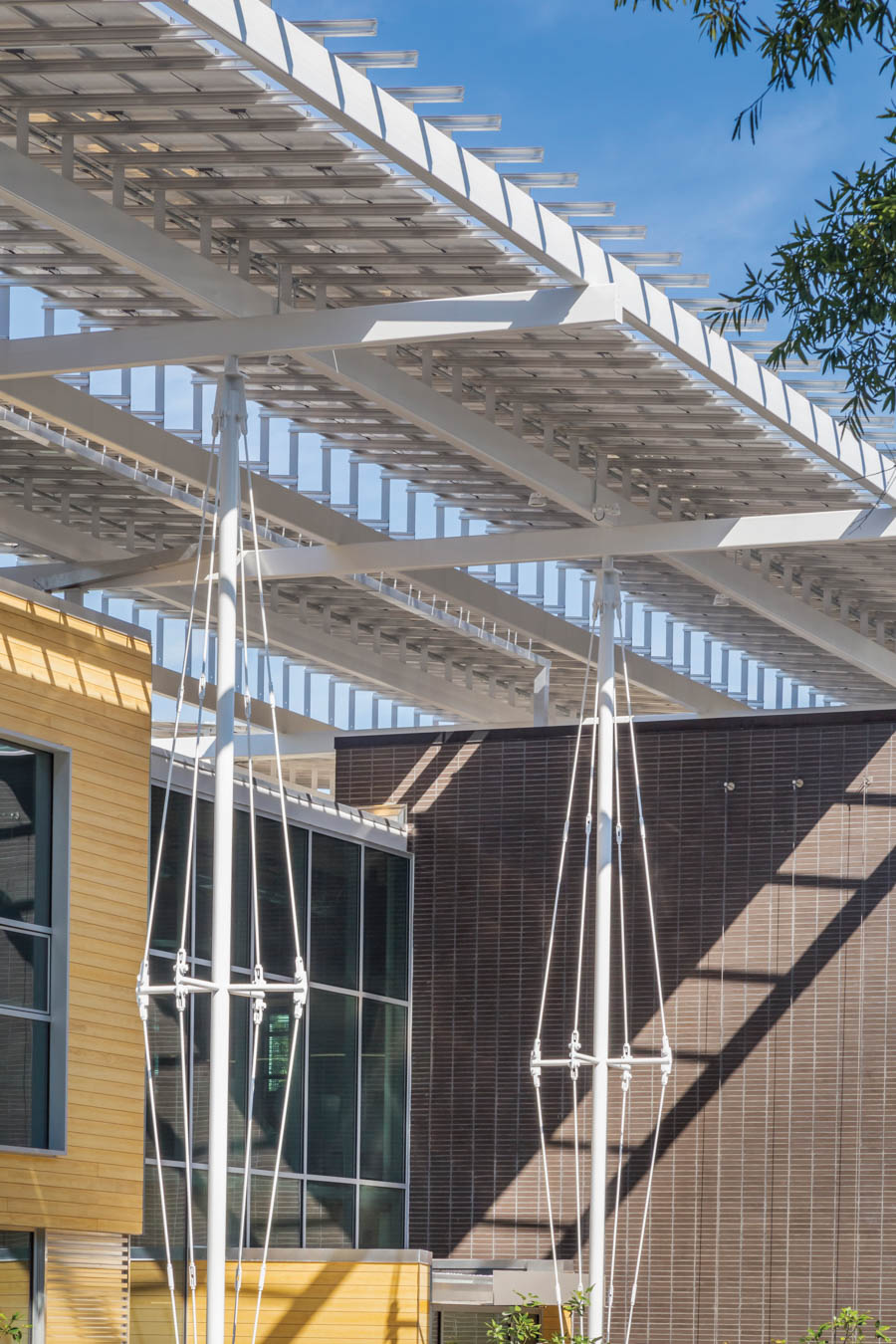
February 24, 2020
Georgia Tech’s Kendeda Building Sets a High Bar for Regenerative Design
The new center is the largest project in the southeast United States to pursue Living Building certification, widely regarded as the industry’s most rigorous sustainability credential.
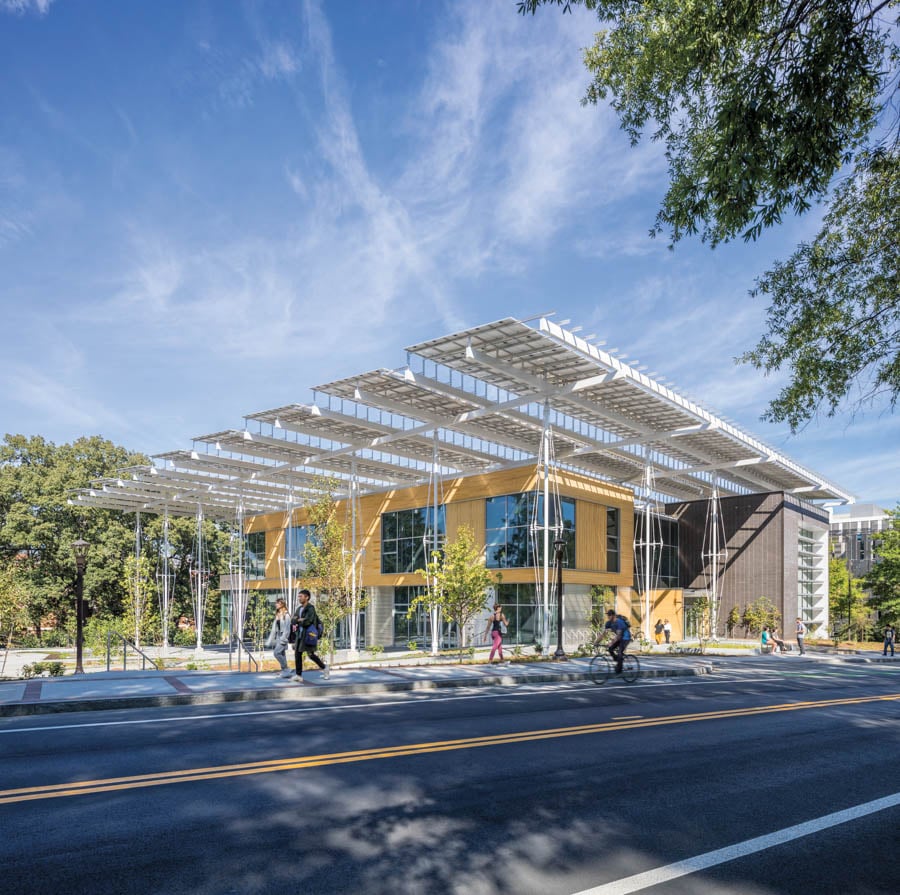
This month, the Kendeda Building for Innovative Sustainable Design at Georgia Tech will start its first semester of classes, offering itself to students as an ongoing case study of regenerative building. Situated on a 1.35-acre corner site on the Atlanta campus, the center—made possible by a multimillion-dollar grant from the Kendeda Fund—announces itself with a 917-panel solar array secured to a tensile steel structure, giving the impression of a sail straining against its own lift.
The 46,800-square-foot project is the largest in the southeast United States to pursue Living Building certification, widely regarded as the most rigorous sustainability credential in the industry. When the center does achieve it (which it’s expected to do, along with LEED Platinum status), it will prove that Atlanta’s temperature extremes and high humidity are no barrier to reaching the highest levels of regenerative design—a concept foundational to the Living Building Challenge, which goes beyond sustaining the natural environment to restoring it.
The project owes its success to an integrative design approach, still unconventional for the industry, that brought architects, construction managers, and engineers together as early as 2016; Georgia Tech selected architects Lord Aeck Sargent and The Miller Hull Partnership only a few months before hiring Skanska to manage building.
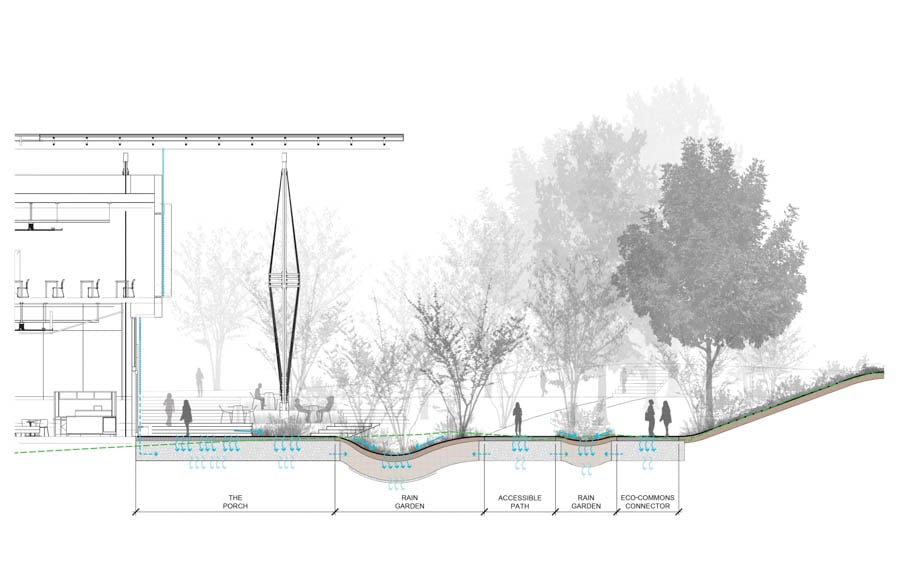
“Without that level of integration, you can’t achieve this idea that everything does more than one thing,” says Joshua Gassman, sustainable design director at Lord Aeck Sargent. “Because everything is so interconnected, everyone had to be there as a part of [the process].”
The idea that design elements would play multiple roles was key to achieving all 20 mandatory “imperatives” of the Living Building Challenge. Take the profile-defining photovoltaic array. Solar was a given; all Living Building Challenge projects must produce more energy than they consume. (To do this, the team reduced the building’s energy load—using strategies like shading, triple-pane glazing, stacked ventilation, and radiant heating—and relied on the campus metering system as a “battery” to accept, store, and provide excess energy as needed.) But the Living Building Challenge also calls for the project to collect and treat water on-site. The team came up with a roof design that would not only support a large-enough array and collect rainwater (for an estimated 460,000 potable gallons annually) but also shade spaces below, ticking off the requirements for place-making and beauty along with energy and water.
This multifaceted approach continued inside as well. The Living Building Challenge’s equity imperative led to a central universal-access ramp in the double-height, atriumlike main hall. The team stepped the building in 30-inch increments to seamlessly connect with the site’s existing topography, allowing ADA access to be “the primary path, the most desirable way to get through the building,” says Brian Court, a partner at Miller Hull. The ramp is a focal point in the open, community-oriented space, whose roughly 40-foot height also helps circulate air, supporting thermal comfort. It’s a fitting approach for a space that forms the heart of the building, providing connection and access to the surrounding labs, classrooms, and offices.
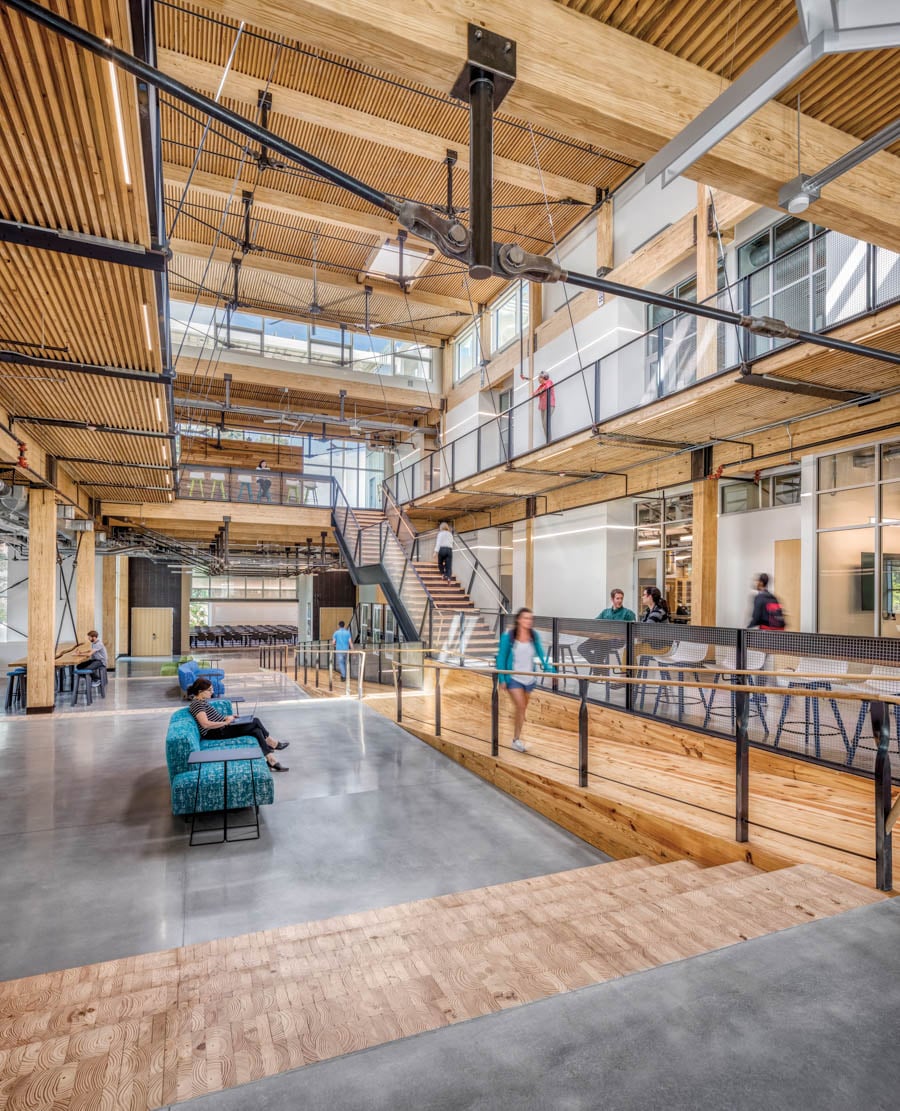
Another requirement, a ban on Red List materials (including BPA, many flame retardants, and PVCs) to the extent possible, also opened design doors. The project team had elected to use a timber-frame structure, widely considered a more sustainable option than steel or concrete from an embodied-carbon perspective. But timber-frame beams and columns use Red List adhesives—something the Living Building Challenge acknowledges as a market reality. To reduce the amount of adhesives in the project, the team found it could use nail lamination rather than glue in the floor decking, and decrease reliance on new wood by upcycling 2x4s from Atlanta’s film-industry sets.
Getting the 2x4s from Lifecycle Building Center, a local nonprofit, was relatively easy, but since they were salvaged, they couldn’t be used to bear structural loads. Skanska devised a solution that would use the reclaimed planks as spacers within a nail-laminated decking panel. The challenge came in finding a subcontractor to fabricate the unit. “No one had salvaged wood into a timber structure before in this manner,” says Jimmy Mitchell, sustainability engineer at Skanska. Eventually, the team realized the only realistic option was to build it in-house. That, too, opened a door.
“We had the ability to do something different because we were doing it ourselves,” says Mitchell. “We partnered with Georgia Works!, which is a local workforce development program for formerly incarcerated men.” Skanska’s early involvement led to other critical choices, like using CarbonCure in the concrete foundations to offset their carbon emissions, and repurposing crosscut offcuts from the wooden decking to finish the main hall’s occupiable stairway. And the firm played a crucial role in managing what was arguably the most difficult part of avoiding Red List materials: overseeing two rounds of submittals to ensure that only specified items were on the construction site. “What we love so much about the Living Building Challenge is rather than looking at specific requirements, it’s a holistic look at designing and building,” says Court. “I like to think of it as instead of designing a building in a linear sense, you’re looking at a set of problems and trying to solve them organically, the way nature evolves.”
You may also enjoy “As Above, So Below: The Reception Pavilion for the National Assembly of Quebec Digs Deep.”
Would you like to comment on this article? Send your thoughts to: [email protected]