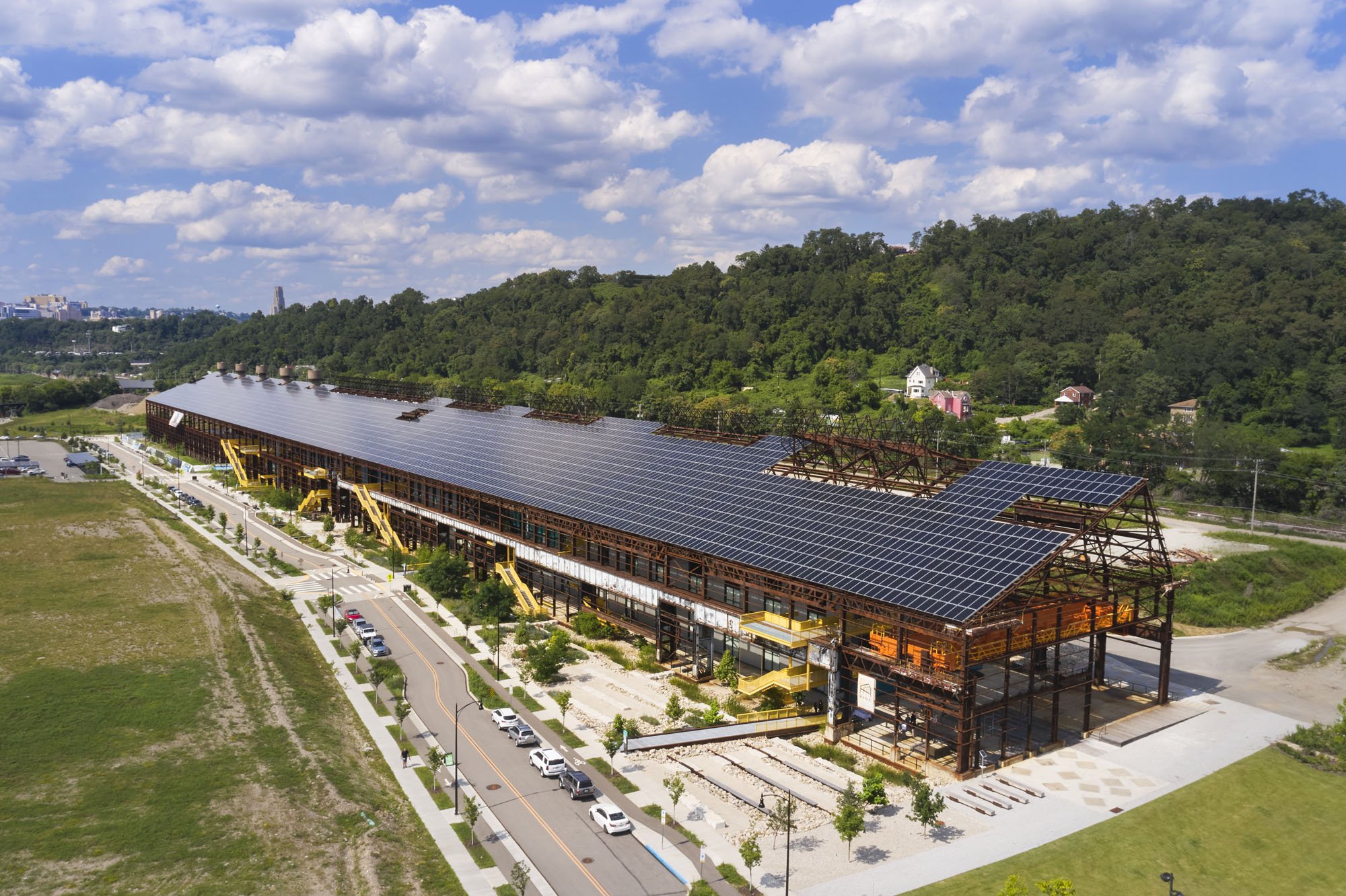
May 1, 2023
Pittsburgh’s Mill 19 Is a Postindustrial Innovation Hub
The Hazelwood section of Pittsburgh, which hugs a U-shaped curve in the Monongahela River, was once a pivotal center in the city’s steel empire. Along the riverbend stands Mill 19, a narrow former factory that is nearly one-third of a mile long. It was once occupied by LTV Coke Works, which closed in 1997, making it the last steel mill to operate within city limits. Today, Steel City’s continuing renaissance into an industrial hub for robotics and AI tech is thoroughly embodied in the gut renovation of Mill 19 by MSR Design.
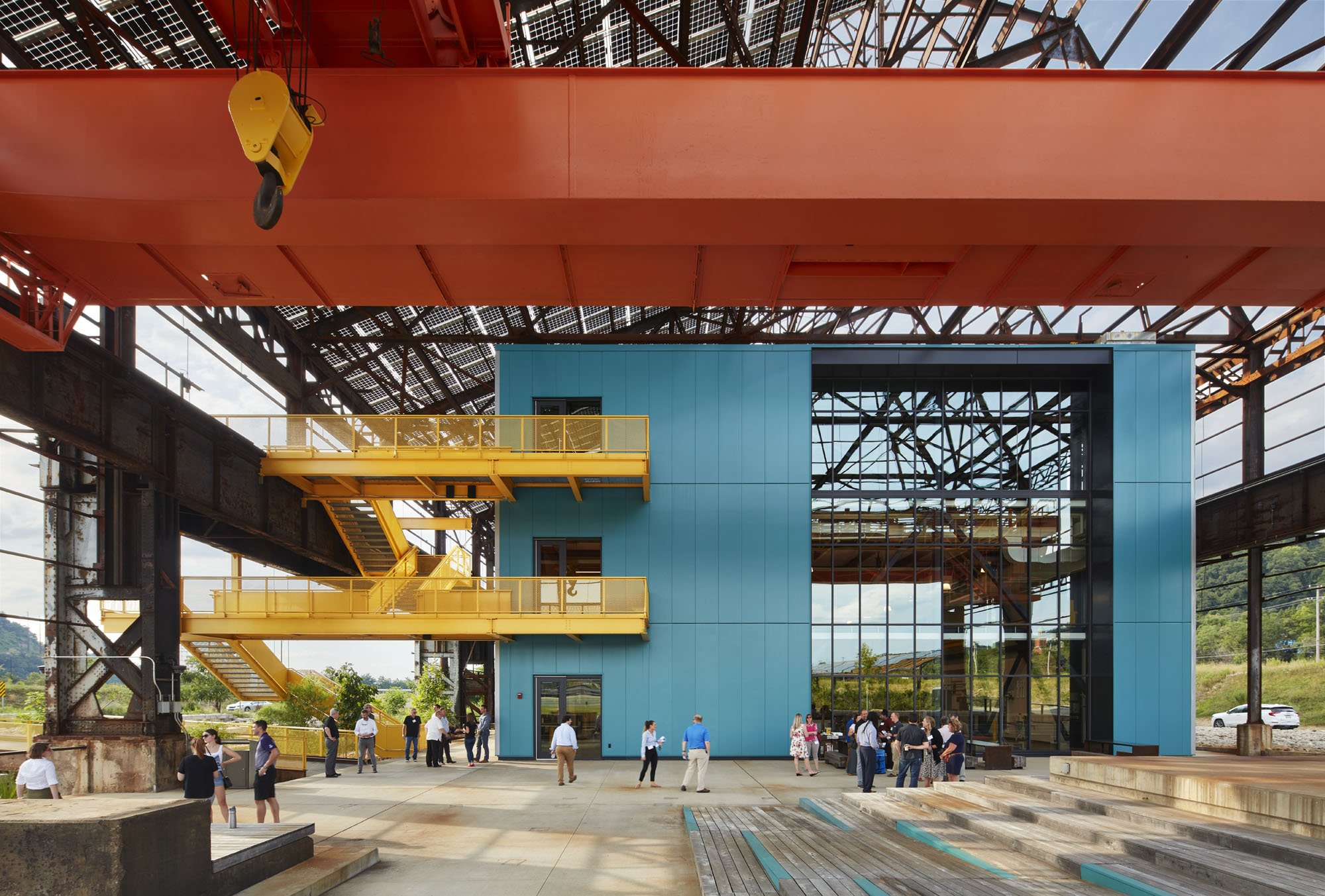
Reinvention and Remediation at Mill 19
“It’s an iconic building that gives the whole site a presence you couldn’t otherwise create,” says Don Smith, president of RIDC, the site’s developer. Of course, it would take a pair of rose-tinted glasses to see the redevelopment potential in such an industrial ruin, not to mention transforming it into a place that attracts collaborative, in-person work. The remediation was extensive, says Smith, including lead paint and asbestos abatement, filling existing underground tunnels, and removing the mill’s 18-inch-thick concrete slab, 100-percent of which was broken up and repurposed for landscaping and public realm interventions.
“There really wasn’t anything you could call architectural on the site. It was blast furnaces and railyards and slag heaps. But that kind of abandonment was interesting to us,” says Tom Meyer, cofounder of design architecture firm MSR Design. “The shed, of course, is this enormous artifact worth keeping.”
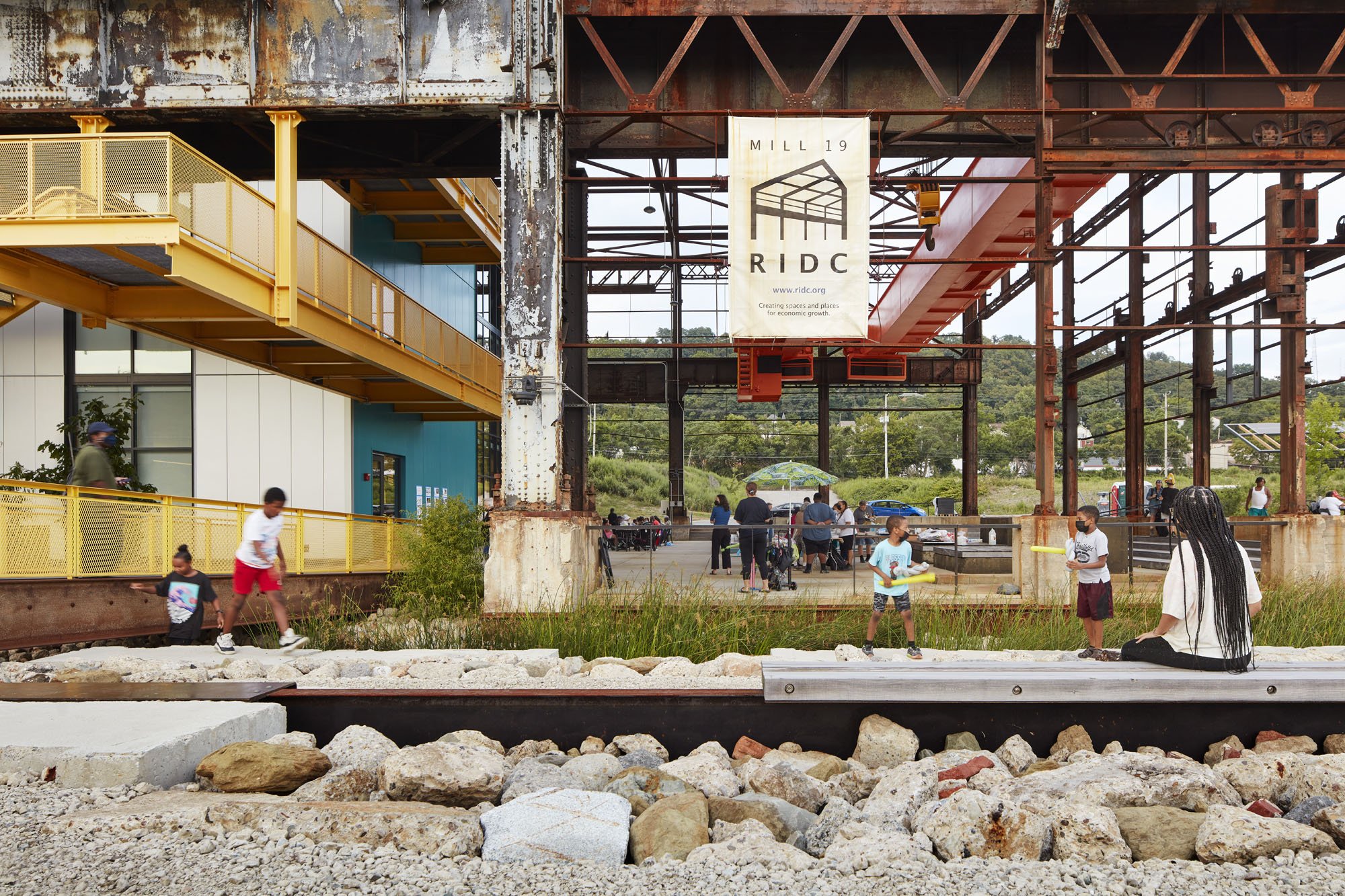
MSR Design Repurposes the Mill’s Massive Steel Frame
All that remains of the old mill is its shell. Its roof and siding were completely removed, and the frame now supports the largest single-slope photovoltaic array in the country, generating two megawatts annually. Within the exoskeleton of steel girders—completely decoupled from the shell—are three office buildings, each equipped for tenants in the high-tech and manufacturing fields. Building A, the largest of the three, was completed in 2019 and is home to Carnegie Mellon University’s Manufacturing Futures Institute and the associated public-private consortium Advanced Robotics for Manufacturing Institute (ARM), which occupy the first two floors of the 450-foot-long building. Building B, the smallest of the three, at 300 feet long and completed in 2020, also happens to be home to the development’s largest tenant, the autonomous vehicle company Motional, which occupies the interior ground floor. The final phase, the 400-foot-long Building C, to be completed later this year, is subdivided into multiple tenant spaces, resembling a more traditional take on the commercial office building. Passages between the buildings and walkways add porosity to the site and help define it as a campus for next-generation private enterprise and public engagement.
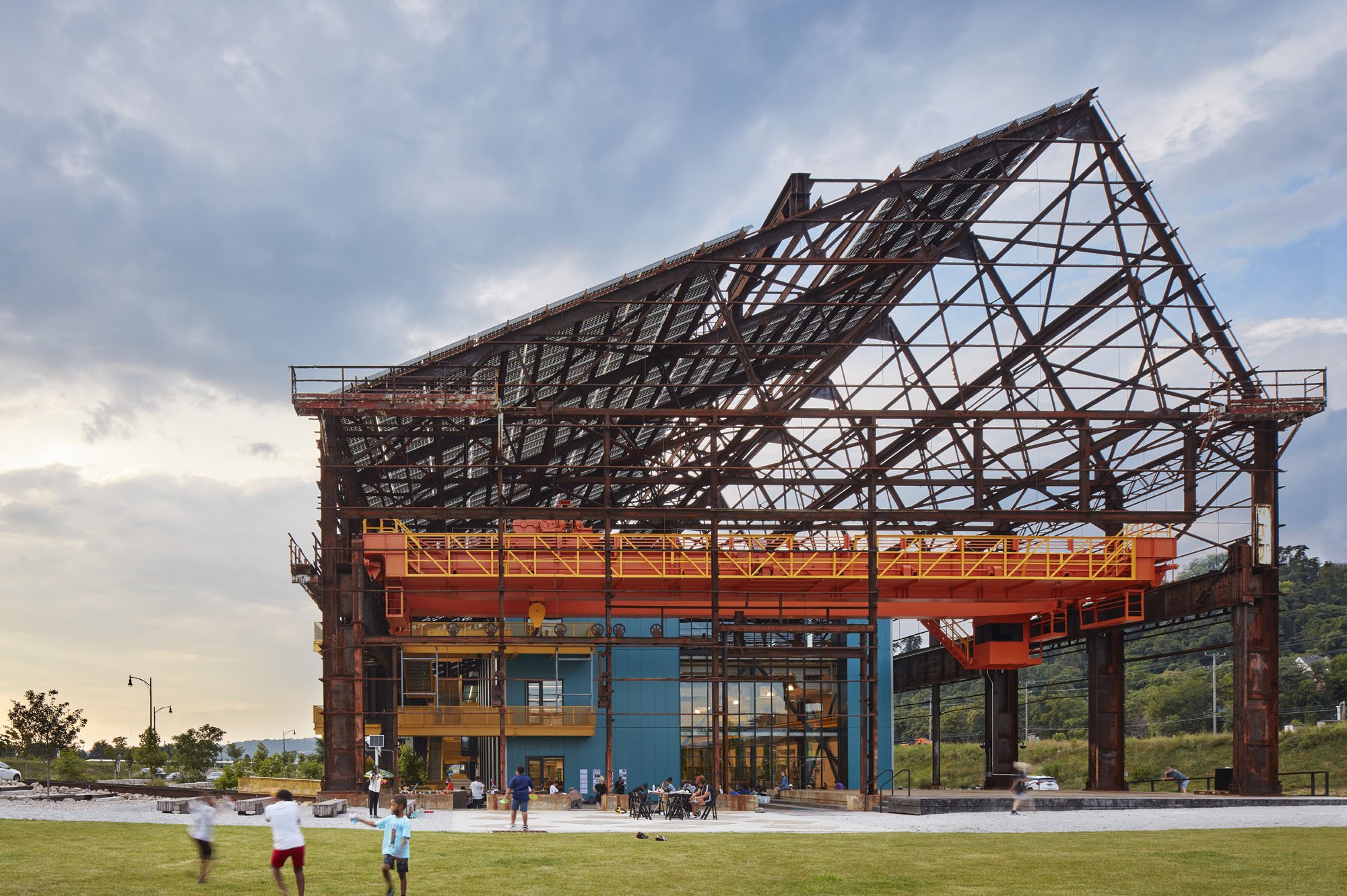
New Possibilities for Steel City
The reinvention of Mill 19 could have gone several ways. Heavy manufacturing and industry were discounted due to their energy intensity, and storage and other low-density activities would have done little to revitalize the neighborhood. According to Jeryl Aman, the project manager and architect with MSR, “There was a lot of concern about how this new development would knit into the existing community.” As happened in most Rust Belt towns, when industry packed up in Pittsburgh, widespread disinvestment depleted populations, livelihoods, and disenfranchised generations of residents. To right some piece of that wrong, Mill 19 needed to do more than attract high-profile tech outfits; it had to be accessible and regenerative. “RIDC set an agenda for a very sustainable community, one that’s in line with the future of Pittsburgh,” says Meyer.
As it supports a mix of buildings and public spaces, the project is extremely energy efficient. There is no combustion on site, the solar array meets most energy needs and filters daylight through its glass panels. Meanwhile a central mechanical plant provides a shared water loop for heating and cooling, and stormwater is collected on site and directed either to cisterns for non-potable use or to a 12-foot-wide channel that runs along the west side of the building. Rather than allow stormwater to infiltrate already contaminated soil, the channel is fitted with an impermeable liner that allows water to flow northward into a retention pond.
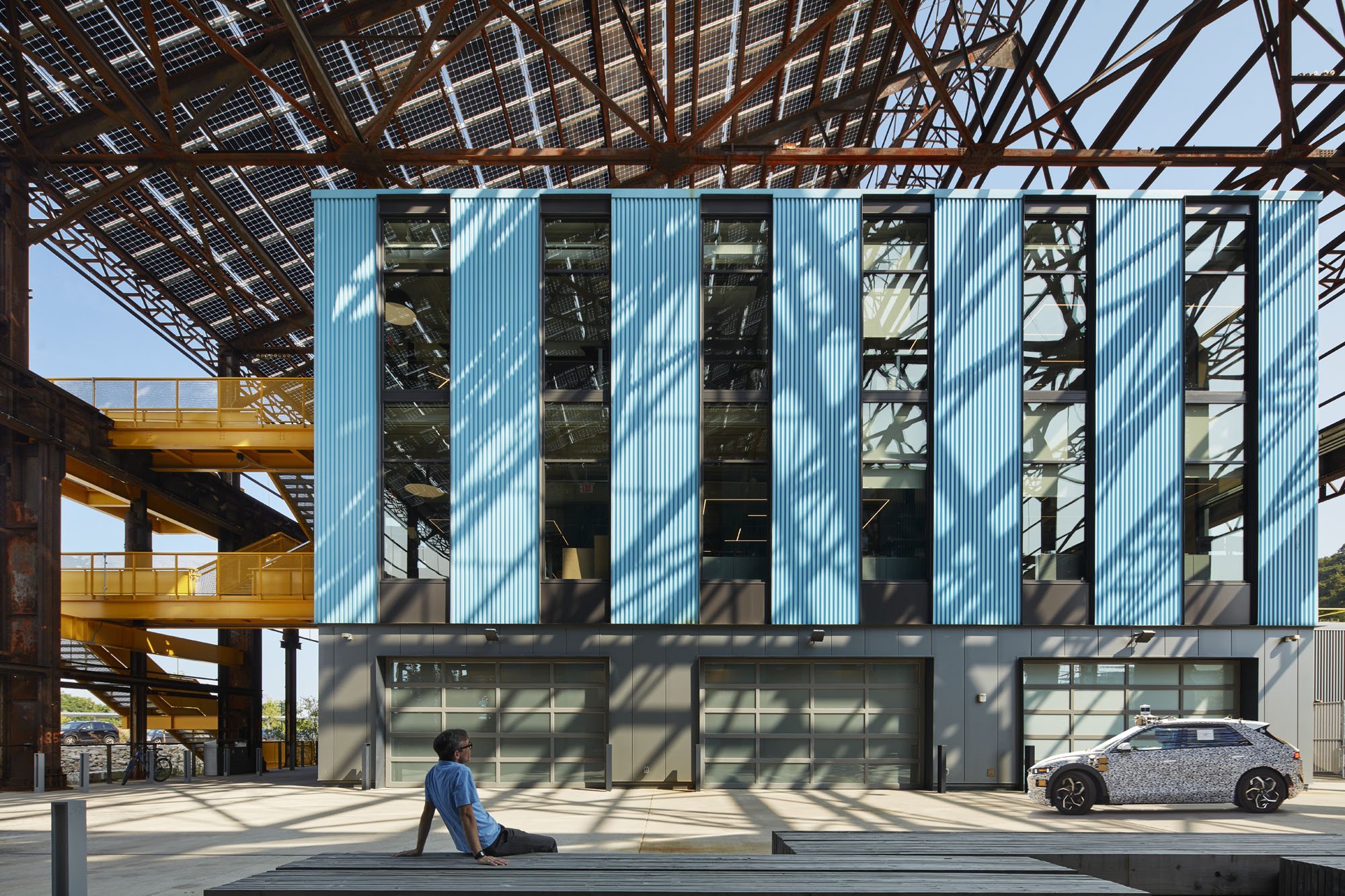
TEN x TEN Designs a Garden Made of Rubble
Salvage and reuse were crucial factors as well. Bunker blocks, sliding door frames, structural C-channels, railroad tracks, and even a 40-foot crane were all repurposed. But the most substantial of these efforts concerned the concrete slab itself. Landscape architect Maura Rockcastle, of the firm TEN x TEN, calls this the “rubble strategy.” The existing slab was broken up into various sizes for multiple uses, some a gravelly blend of large chunks that line pathways and add definition to the public realm, and others into a “sort of ruderal mulch” that naturally attracts volunteer plant life. The “disturbance adaptive” plant palette includes more than three dozen robust and fast-growing species of trees, sedges, and wildflowers.
Rockcastle takes note of the mill’s sculptural form, which she considers more of a landscape component than an architectural one. There’s something to this. Three new, high-profile office buildings are discreetly tucked into the depleted husk of an old mill. On their own they’re outstanding, but they’re not the main attraction. The site itself is. And if Mill 19 is to become that catalyst for community revitalization, as RIDC intends, maintaining the integrity of that public piece is critical. “We wanted to restore the site to productive use, and make sure it was done in a way that is environmentally, socially, and economically sustainable,” says Smith. “There’s a lot of ability to grow in Pittsburgh without displacing.”
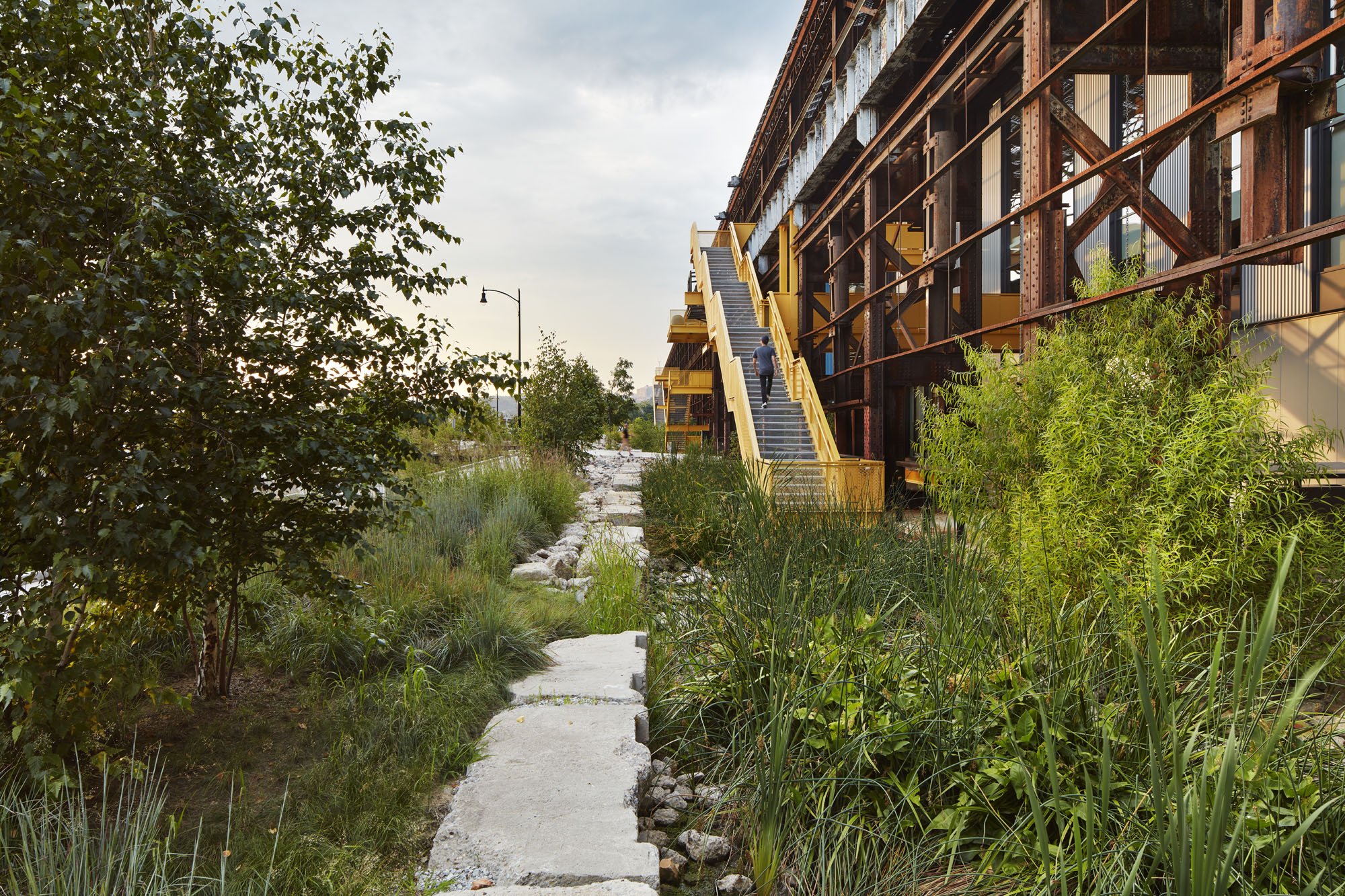
Selected Sources:
Design Architect: MSR Design
Developer: RIDC
Environmental Design Consultant: Atelier Ten, Inc.
Structural and MEP Engineering: Bala Consulting Engineers
Civil Engineering: Lennon Smith, Souleret Engineering, Inc.
Graphics: MSR Design
Landscaping: TEN x TEN Studio
Lighting: Gallina Design, LLC
Associate Architect: R3A Architecture
Technology Specialist: True North Consulting Group
Cost Estimator: Project and Construction Services
Cladding/Facade Systems: Morin, Kingspan, Centria, Metal Sales
Glazing: Vitro Architectural Glass
Windows: EFCO
Conveyance: Schindler, TKE
Would you like to comment on this article? Send your thoughts to: [email protected]
Related
Viewpoints
The Salvage Manifesto: Harness the Power of Material Reuse
Developed during the METROPOLIS Circular Future Hackathon, this manifesto explores the urgent need to invest in building material salvage to combat waste and environmental degradation.
Viewpoints
Dream Jobs for a Circular Built Environment
Developed during the METROPOLIS Circular Future Hackathon, this tool evaluates reuse and recycling potential, empowering sustainable decision-making in the specification process.
Viewpoints
The Circular Buildings Podcast
Developed during the METROPOLIS Circular Future Hackathon, this tool evaluates reuse and recycling potential, empowering sustainable decision-making in the specification process.