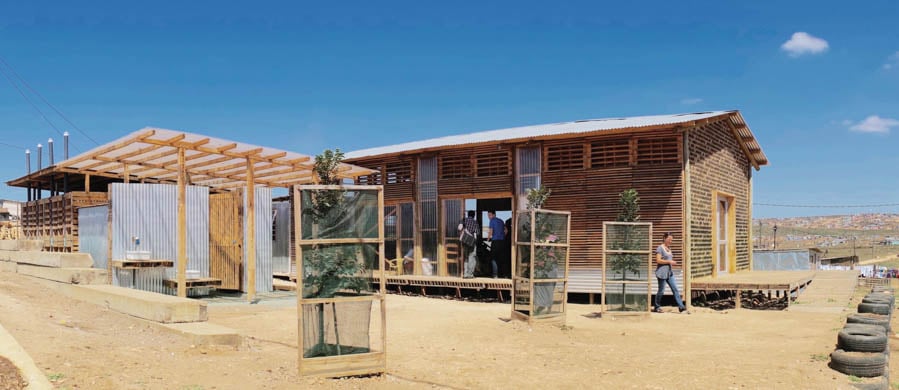
August 19, 2020
Game Changers 2020: Kevin Kimwelle and ICON on Social Equity in Building
In the first of four pairings of our annual Game Changers series, a South African architect and Texas construction company share the goal of making housing cheap, accessible, and livable for all.
As era-defining events continue to unfold around the world, digital platforms have catalyzed civic debate as never before. So for our annual spotlight on Game Changers—that is, the practitioners and researchers reshaping the A&D field—we used videoconferencing to connect people from different parts of the globe and from disparate spheres of design. Over one-hour sessions, our Game Changers discussed social justice, health, technology, and urban place-making—all topics implicated in the maelstrom of 2020. In the following text, we recap highlights from those conversations. An important takeaway is that our most pressing problems must be solved through interdisciplinary, networked approaches.
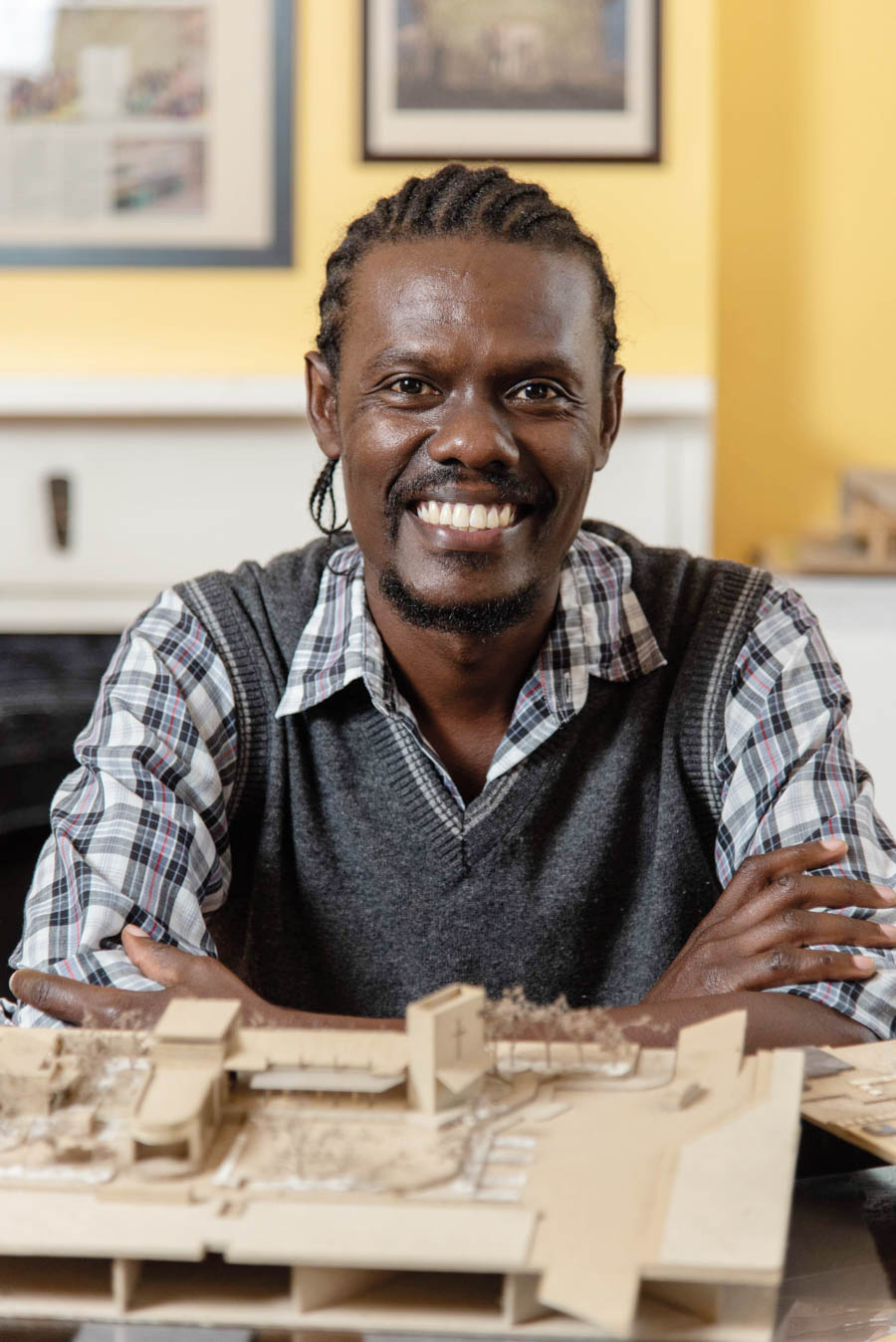
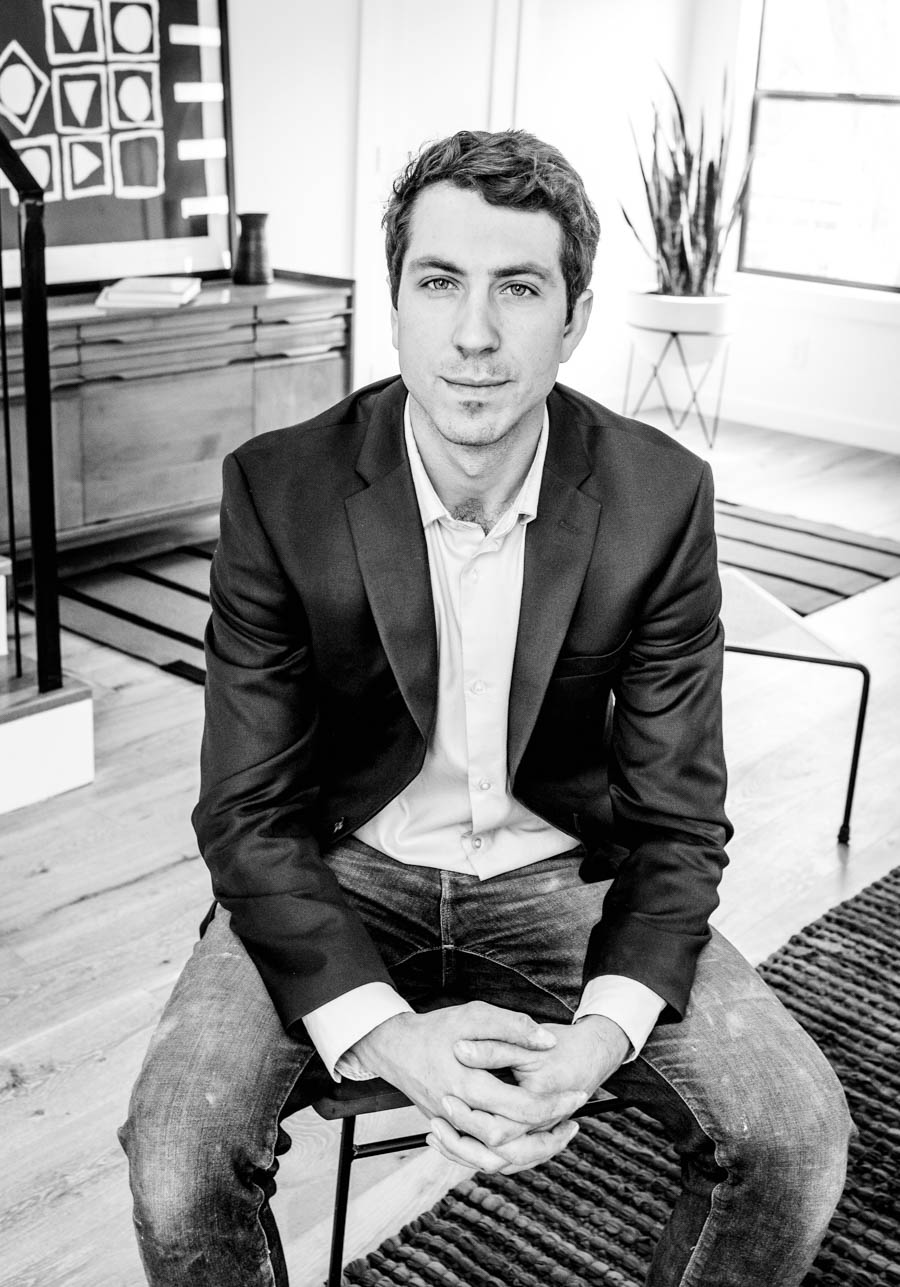
Imagine two design-driven entities separated by continents, cultures, and a seven-hour time difference arriving at the same approach to the housing crisis: Bet everything on one radical construction method and build it for the truly underserved. That’s what ICON, a Texas construction company, and South Africa–based architect Kevin Kimwelle did.
In the case of the Austin builder, the gamble is 3D-printing concrete to create houses for poor and working families. For Kimwelle, the leap of faith is channeling his formal architectural training to transform trash into functioning, welcoming schools. Both saw desperate need around them, and despite working in industries driven by deep-pocketed clients, they’ve prioritized the disenfranchised over profits. But is good design good for business when clients can’t pay? How can these professionals thrive, given the challenges they face? Metropolis connected them for a special conversation to learn their shared traits.

KEVIN KIMWELLE: I studied architecture and was happily practicing normal, mainstream architecture. But I did this overland trip through Africa, and I guess I was also discovering myself. In doing this trip, I came across a lot of poor, marginalized communities between Nairobi, Kenya, and Port Elizabeth, South Africa. And I kept wondering what I could do: Is there something we can do as designers or architects, especially when most of mainstream architecture is geared toward communities that can afford it?
I started just digging up [information] about social innovation, [ways to] design for communities that cannot afford architects. And what began slowly as exploration ended up being something that I had to get into full-time. There was very little [help] from within my community of practitioners. It felt as though these communities were forgotten. So that’s how I got into it. The beginning was just bit by bit, and discovering myself as I discovered this architecture. Building faith, and hope, and trust, and connections, and networks, and eventually it’s grown over the past couple [of] years. It’s something quite remarkable, I think. How about you guys?
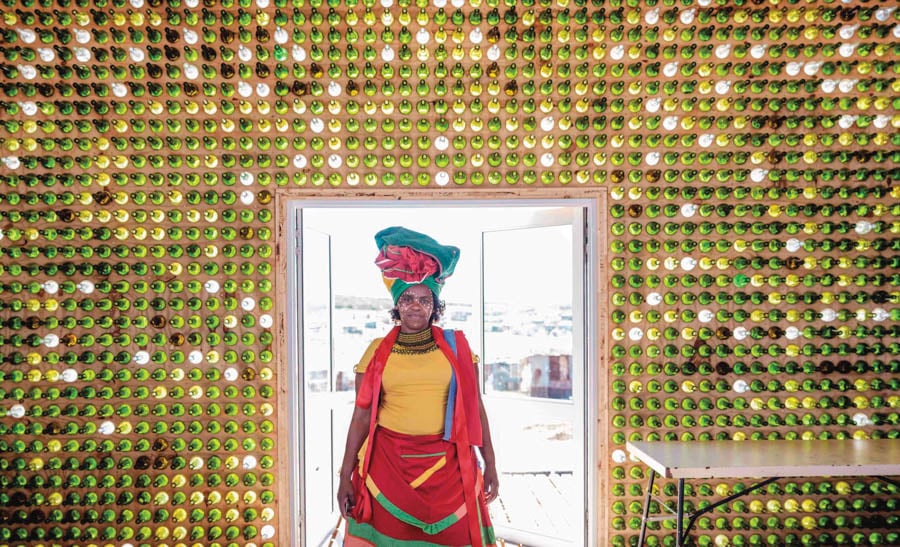
ALEX LE ROUX: I have a technology [background]. I started about six years ago, looking at the way small plastic 3D printers worked. You might have seen these before; you can print all sorts of little gizmos and gadgets.
I thought the technology was untapped. I thought if we made the machines a lot bigger and used [slightly] different material, perhaps there were new things we could print. I started experimenting with bigger machines. I went literally into the backyard and built the biggest frame for a 3D printer that I possibly could—about ten feet by ten feet by ten feet. It wasn’t pretty, but I’m still proud of it. And eventually, like you might squeeze a [tube] of toothpaste, I was able to create a little structure. That was enough for me to think that there was something there.
So that led me on a five-to-six-year journey to get to where we are today, which is [having] 3D-printed 16 homes in Mexico and Texas for all sorts of different customers—a lot of people in underserved communities, as well as middle-market housing. These are houses valued at $300,000 to $500,000 or so. We’re just really excited about the potential for this technology. Every day someone new calls us up and asks us, “Hey, can you do this new thing with the printer?” And we’ll think about it a little bit, and then we’ll say, “Actually, we can.” That’s pretty cool that we’re just constantly finding these new use cases. And I guess it makes sense. We’ve got a giant 3D printer. They’re able to make almost anything. There’s just a ton of versatility about what these machines can do. So we’re really excited about the future.
DMITRI JULIUS: I came to ICON specifically for that mission of trying to make an impact in those underserved communities. I came across Alex and Jason when this project was still in its early stages, where they were closing a round of funding and establishing a mission of “We want to take the opportunity to use this technology to minimize human suffering, and make a meaningful dent in the global housing crisis.” And a light went off that this is what I need to be doing. I was born into one of those communities of color in South Central L.A., and always in the back of my mind, I understood that sense of ownership, that sense of pride didn’t exist in [my] area because housing was so inaccessible to so many people based on a multitude of factors, but primarily cost. So I beat down Jason and Alex’s door until they hired me, and here we are.
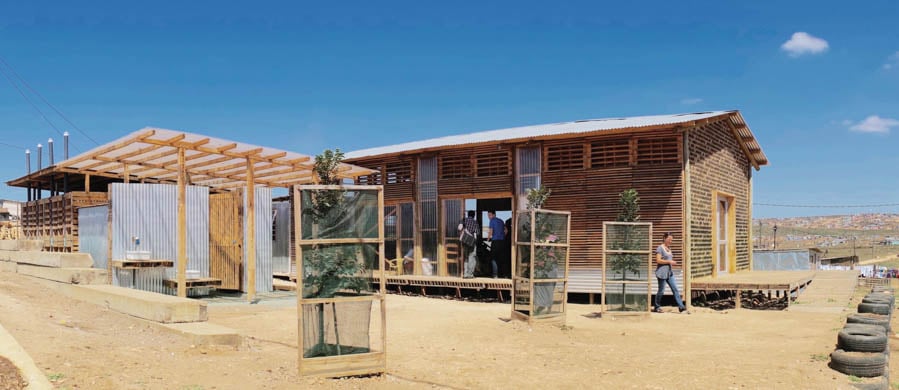
KEVIN KIMWELLE: Port Elizabeth is an industrial city. I would compare it to Detroit, Michigan, actually. It feels like Detroit is our sister city. The motorcar industry is a big driver of the economy here, and as a result, there’s a lot of industrial waste from the [manufacturing of ] cars, or stuff that leaves South Africa through Port Elizabeth. In a way, I think I was fortunate to have the junkyard at my backdoor.
But over the years—I think it’s been about ten years now—[doing] R&D has helped shift material which was seen as worthless or of no value into [architecture], but more on an experimental level. We find [our work] presently at a space in between mainstream architecture and what you’d call social architecture from a “barefoot architect.” But it’s really what has enabled us to refine our communities. It’s just that I think the sheer scale of need is really big in South Africa.
The need is massive. Government is overburdened by providing sheer basic needs. We fill in, supporting NGOs, charities, churches that need to help communities but cannot afford [architects]. We create some form of temporary architecture through this appropriation of materials until new housing arrives. So actually every, I think, three or five years, we are revising the architecture… either tearing it down because it’s outlived its function or strengthening it.
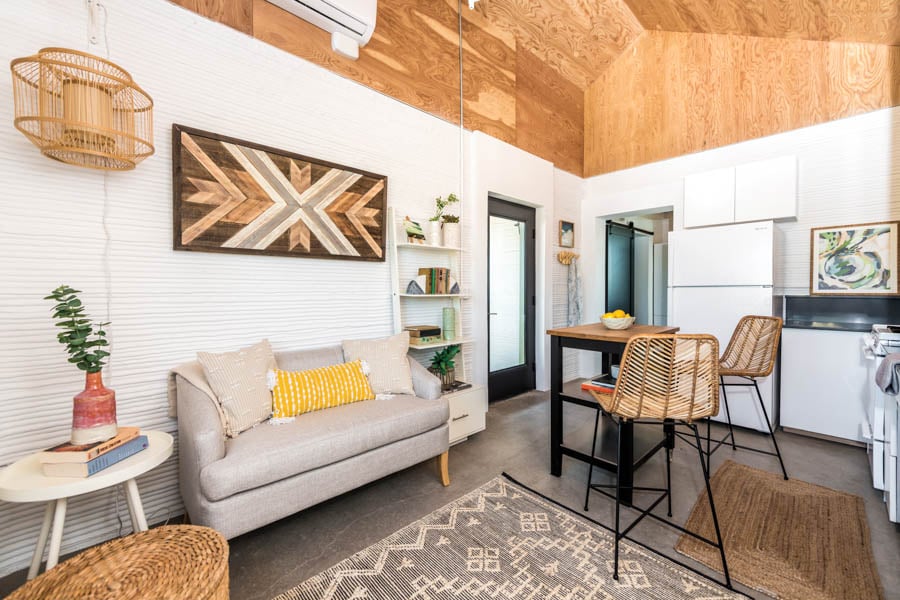
ALEX LE ROUX: Scale allows for so many things to happen. Number one, you start transforming the lives of more than just a few people. The big vision for ICON is thousands and thousands [of houses] across the United States, across the world. That [picture] is so compelling. I think it gets me up out of bed in the morning…. And we’re starting to see that vision slowly realized with the project we’re doing in Mexico, which is slated to be about 50 homes in this particular development. We already have a row of eight homes, and when you see a row, it’s like, wow, that’s starting to be a good number.
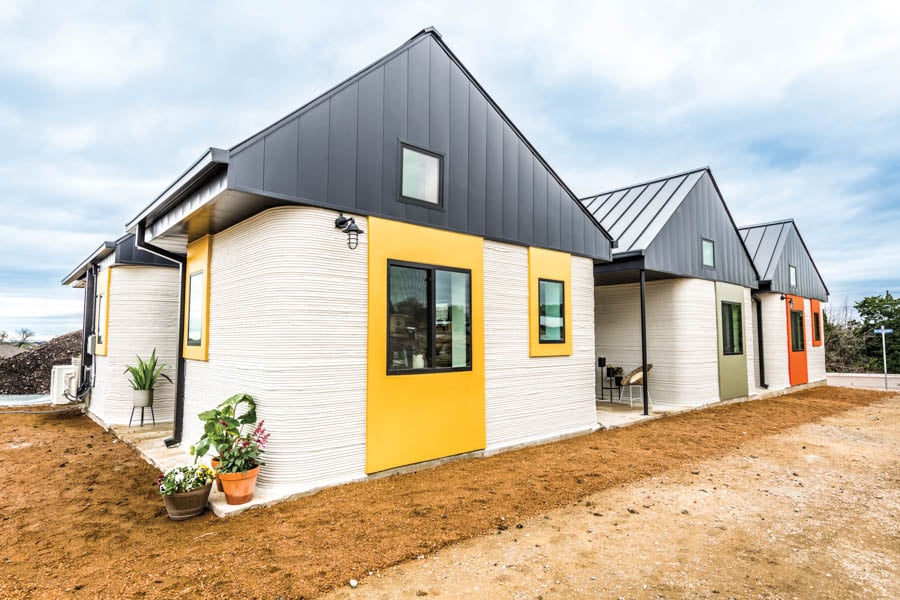
The mind can make that mental jump from eight to 100. Then from 100 you can imagine 1,000. It’s slowly starting to happen. But one of the things we hear a lot with scale with other construction methods is that you have to have everything be the same. This is what you see with manufacturing. Every iPhone has to be the same, or every prefab house has to be the same, because it’s on a manufacturing line. Whereas with 3D printing, each house can be totally different. And that’s not just a cool thing, that is a deeply practical thing. The needs of a community in one part of town might be very different [from] needs…in a different part.
3D printing is very well set up to provide different solutions to different sorts of people at scale. And that’s compelling.
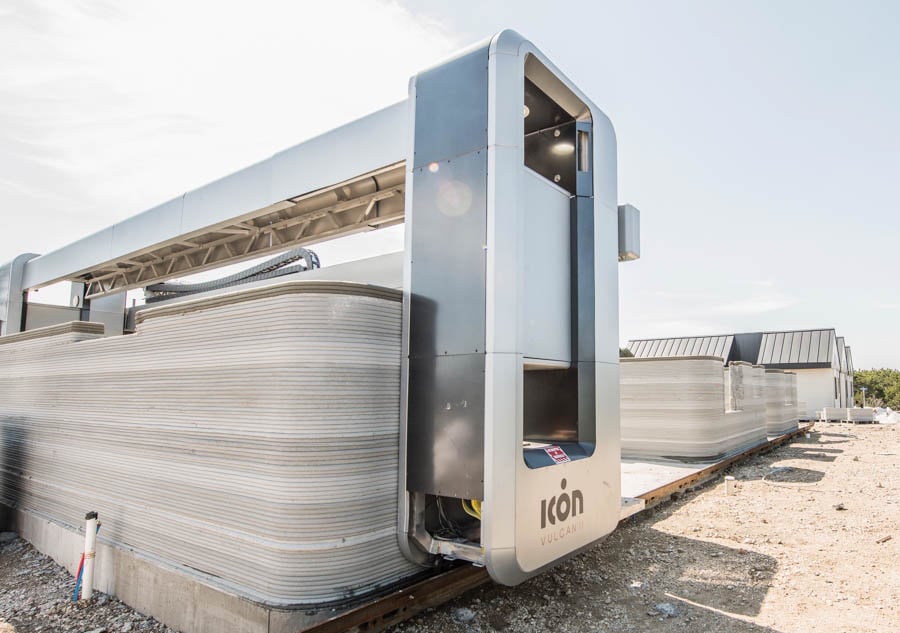
DMITRI JULIUS: There’s something like a 1.2-million unit disparity worldwide when it comes to the lack of housing stock. And so if you utilize the industrial model and continue to build things the exact same way that they’ve been built, it’s clear that what you end up with is a deficit and individuals without housing. And so the 3D-printing technology presents a multitude of interesting solutions. Alex hit on one, which was scale—the ability to have this agnostic-use case to build a single-family home here, and a different type of structure, maybe a hospital or school, there.
But also, to start thinking about a paradigm shift: If what we’re doing with the industrial model has left us over a million units short, even if we were to employ actively all the fantastic trades – people, all the craftsmen, bricklayers, roofers, painters, and gainfully employ them, there would still be a shortage in housing stock. So we have to think critically about not only demystifying the build process to Kevin’s point but demystifying architecture—utilizing this 3D-printing platform to allow people to design different types of structures to [provide] the pieces of the puzzle that are missing from their communities.
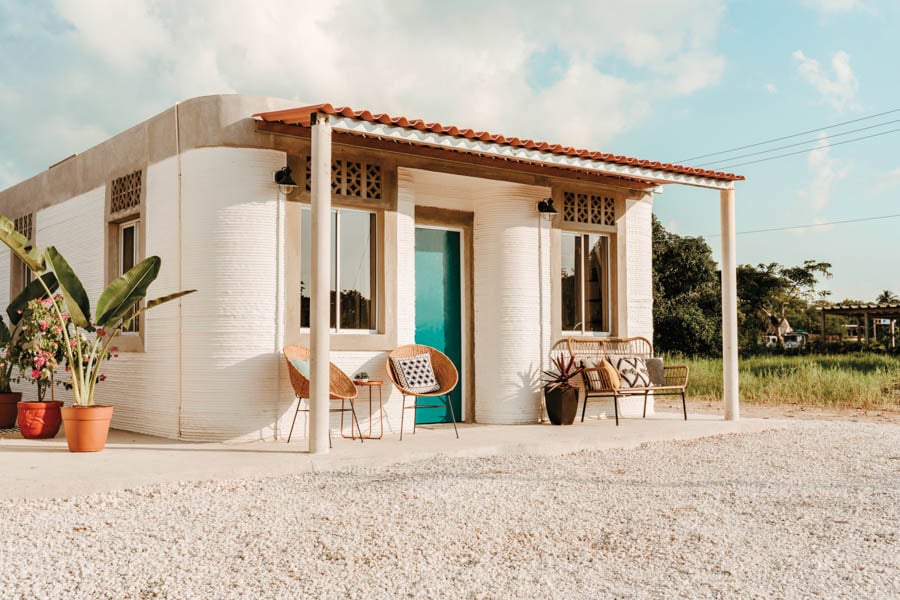
KEVIN KIMWELLE: It’s interesting you say that, because on our end, we’re using [a] concept which works a lot with 3D printers.
The design process is actually done globally. We have a team in Detroit, at Lawrence Tech University, and we have another university in Germany. I’m in Port Elizabeth, and there’s a university in Cape Town…. Every institution or organization tests something different. But because of technology, we’re able to model, to test, and to really pack the thing in a truck. It’s not really a massive truck. We’re able to [send] them in shifts and move them to another part of the world or another part of the country, meet a need, and come back and plan the next one. Even while we are on-site, the next one has been designed by a different group in India. So the technology has enabled us to connect with other parts of the world…which is social. It’s a social need. It’s almost a realization that technology can eventually make us meet that paradigm shift that Dmitri was referring to. We are at a point in the world where we can now all connect and move our energy toward a need of a community and realize it in a month. Previously it would have taken what, years? Get all the donors and sponsors, travel to all the various organizations, and then start…sticking the thing together. Now it’s doable [with] technology.
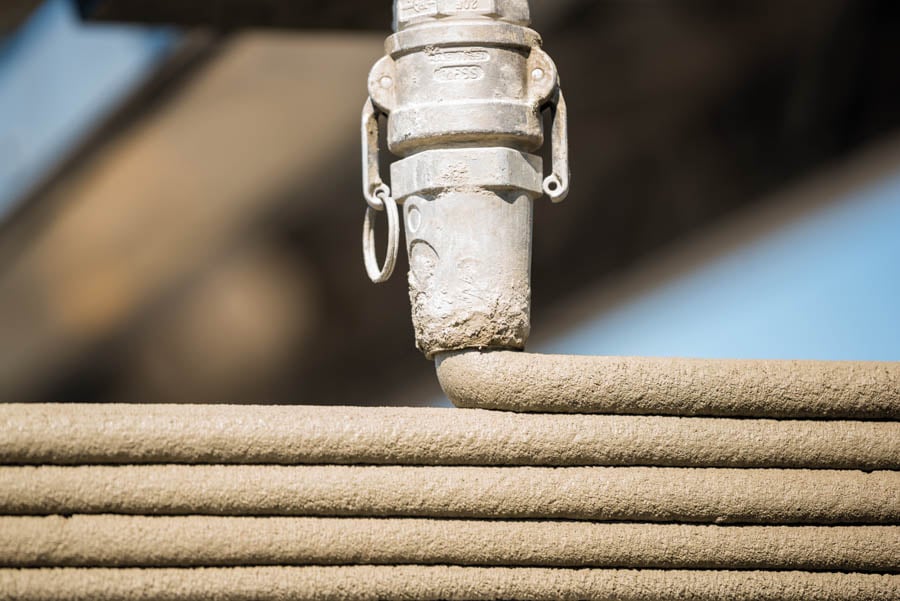
DMITRI JULIUS: Kevin, that’s absolutely right. And when you start talking about the uses of digitally native design files that can accelerate that process and also diversify the uses, you start to see some meaningful gains. We’ve been able to leverage that technology to design structures for our crew in Mexico. That’s the direction that we should be thinking about [for] housing: How can we utilize the connectivity we have to leverage all the knowledge that’s intrinsic to these different communities, to help us rapidly scale up meaningful stock? So we’re mitigating waste, and creating things that are useful, and minimizing suffering.
ALEX LE ROUX: Dmitri hinted at the digital design platform that we’re working on. I can’t share too much information, but the general idea is to start to democratize architecture. People think that you have to engage a big fancy architecture firm to have a custom house. That’s the mental model that people live in. But I don’t think it needs to be that way. Architecture can be simple. Most anyone can engage in this activity and do it well, if they have the right tools. And a lot of people just don’t have the right tools. The software to do this is really complicated. You need a license, and that license is thousands of dollars.
So people don’t engage in the design process. They say, “I’m just going to leave this to some – one else to figure out. I’m going to pay them all this money.” But what if we lived in a world where you could very easily pull up a website, drag and drop a few lines, and you’ve got a design for a house? What if it was that simple? Or what if you could just browse through a list of architectural designs the way you do on the app store for apps? What if it was that simple to find a new architectural plan? 3D printing allows for us to think in that way.
KEVIN KIMWELLE: When you say “democratizing design” in my part of the world, it’s something that is urgently needed. It’s powerful. Simply because, as I said, the need is overwhelming, and if people wait, they wait. I remember one project [in which] we built a lady a workshop. She’d been waiting for a government house for 20 years. And that 20 years can now be compressed into a month. So what about [her community]? They will never be able to afford an architect, not in the traditional sense. But technology is now taking that…veil away and suddenly design is accessible to everybody.
You may also enjoy “Karen Braitmayer, Founder of Studio Pacifica, Weighs in on Accessible Design.”
Would you like to comment on this article? Send your thoughts to: [email protected]
Register here for Metropolis Webinars
Connect with experts and design leaders on the most important conversations of the day.